The living areas in your home are not confined to the living, family,
or dining rooms. We spend much of our free time on hobbies, such as crafts,
woodworking, sewing, painting or other arts, or rebuilding that favorite
‘48 coupe.
While these activities have particular storage requirements suited to each,
there are a lot of commonalities. Here are some things to keep in mind while
organizing hobby rooms and associated storage.
• If you don’t have a separate room to devote to hobby space, look for
space in the spare bedroom, basement, attic, or garage. If you don’t have
a large space to devote to a hobby area, don’t give up. Many times you can
use a corner with great effectiveness. Make use of mobile storage units
that you can roll out when you want to pursue your interests—a table on
wheels can serve as a craft bench, a sewing table, or even a workbench in
the shop.
• Most hobbies require good lighting. Make sure the room or spot you choose
is well lit; try to use natural light effectively.
• Develop your storage plans to make it easy to put things away. A Phillips-head
screwdriver or that spool of light blue thread is not useful if you can’t
find it the next time you need it.
• Make sure you have ample surface area to spread out projects on which
you’re working.
• Make sure there are enough electrical outlets and that the circuits can
carry the amperage load of all equipment you might plug in and have running
at the same time.
• If your craft requires water, locate the activity in a room that has
existing plumbing into which you can tie a new sink.
• Use enclosed storage spaces to protect valuable tools, to keep fabrics
clean and dry, or to keep Kitty out of your yarn.
• Organize tools or supplies in relation to each other, blades with saws,
nuts with bolts, needles with thread. Use pullout bins or compartmentalized
drawer storage cabinets to sort and store such small items as nuts and bolts
or beads and other craft supplies.
• Think safety. Store hazardous materials or dangerous power tools where
children or pets cannot get to them.
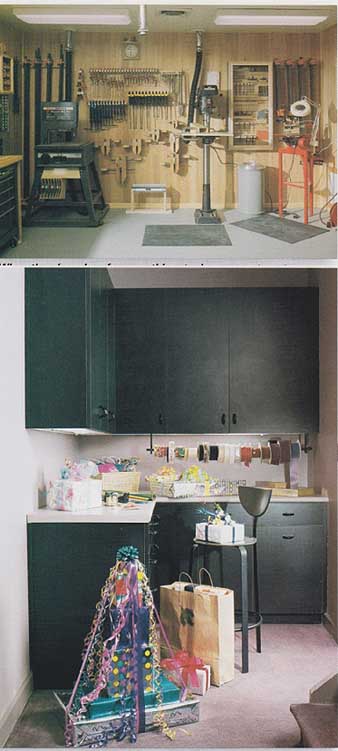
(top) When there’s a place for everything, tools are easy to put away—
and to find the next time you need them. This woodworker’s shop allows the
owner to focus on woodwork, not on hunting for tools. (bottom) Kitchen cabinetry
makes a hobbyist’s craft area look like a professional’s workshop. Cabinets
pack all the essentials: storage, work surface, and lighting. When using
cabinets, be sure to design the countertop surface at the correct height
for the work you’ll be doing.
BUILDING A WORKBENCH
Every workshop requires some kind of workbench. If you don’t have room
for an extensive shop, your bench can be as simple as a flush panel door
placed across a set of sawhorses; they can go back in a corner when you’ve
finished a project. At the other extreme, you can purchase complex benches
designed for professional woodwork. Here’s a bench that falls in between.
You easily can make this bench in a day, and you can make it as complex
as you want. Use the dimensions given here or adapt them to your needs.
Benches generally range from 6 to 8 feet long and 24 to 36 inches deep.
The height of the benchtop should be 30 to 40 inches, whatever is a comfortable
working level for you.
Assembling this bench is a matter of cutting stock materials and screwing
or nailing them together. In this design, the rear legs extend 3 feet above
the bench to serve as a framework on which to mount perforated hardboard,
so you can store your tools right in front of you. Connect all the leg supports
with 2½-inch lag screws for added support. Also, if you make the bench more
than 6 feet wide, use 4x4s instead of 2x4s for the legs.
Make the top out of a double layer of ¾” plywood, covered with ¼-inch tempered
hardboard. The plywood makes a stable surface that won’t warp and the hardboard
provides a smooth surface you can replace when it wears out. If you want
to make the bench fancier, you can build a cabinet or drawer unit into the
area under the bench. Then you would have enclosed storage for expensive
or delicate tools. A locking cabinet would protect your treasured tools
from your curious kids and mooching neighbor.
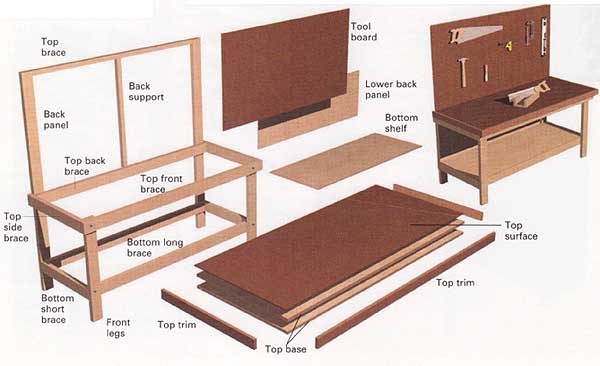
Workbench, exploded view.
MATERIALS LIST |
Item |
Material |
Length |
Qty |
Top trim
Top trim
Rear legs
Front legs
Top front brace
Top back brace
Top side braces
Bottom long braces
Bottom short braces
Bottom shelf
Lower back
Top, base
Top, surface
Top brace
Back support
Tool board |
2x4 pine
2x4 pine
2x4 pine
2x4 pine
2x4 pine
2x4 pine
2x4 pine
½” plywood
½” plywood
¾” plywood
¼” hardboard
2x2 pine
2x2 pine
1/8” perforated
hardboard
1x3 hardwood
1x3 hardwood |
72”
33”
72”
69”
28½”
66”
25½”
25½x69”
22½x69”
30x72”
30x72”
62”
39”
36x73½”
73½”
30¾” |
2
2
1
1
2
2
2
1
1
2
1
1
1
1
1
2 |
2½” lag screws; 3d and
6d finish nails; white carpenter’s glue |
BUILDING A FOLD-DOWN SEWING TABLE
Storing your sewing machine in its own convenient center will make using
it more pleasurable. This sewing center not only puts the machine at your
fingertips, it also provides a handy work surface.
The heart of this project is the fold-down sewing machine shelf. The materials
list and drawing show everything you need if you’re going to build the entire
cabinet. Or you can build the fold-down sewing shelf into an existing bookcase.
Most sewing machines require a space 9 to 10 inches deep, so a common 12-inch-deep
bookcase would be an ideal home for the sewing shelf. The plans here are
for a 3-foot- wide unit, which is also a common bookcase size. Another option:
Build the unit into a spare closet for a true hideaway system.
If you’re starting from scratch, build the cabinet as you would any bookcase,
using the dimensions in the material list. Use rabbet joints at the corners
and install the one fixed shelf (the highest one) by cutting dadoes into
the sides of the cabinet.
The fold-down work surface opens to reveal the sewing machine in its stored
position on a fixed shelf. Other supplies can be stored in cabinets under
and above the work surface.
Before installing the sewing table, determine the most comfortable working
height—usually between 26 and 28 inches from the floor, Test the height
with your machine placed on a trial surface. Make the table wide enough
to hold your machine comfortably; here we use 30 inches.
The flat, fold-down work surface can be marked with a grid that is convenient
for layout and pattern work. Using this design requires that you lift the
sewing machine from its storage shelf onto the fold-down work area when
you want to use it, then lift it back to its storage area when you’re done.
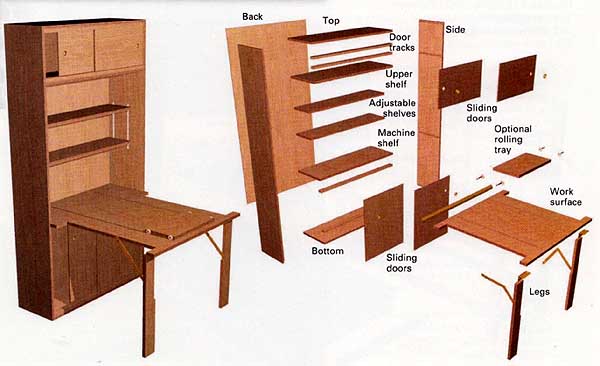
Sewing Table, exploded construction view
--
EASY ALTERNATIVE
Incorporating a movable tray will allow you to glide the machine out to
its work position. The tray rolls along grooves routed into the surface
of the shelf and the worktable. It eliminates the lifting, but this system
has a small drawback: The tabletop then is not a smooth workplace. But if
you use the machine frequently and have to put it away after each session,
the added convenience may make routing the grooves and doing the extra construction
worthwhile.
Make the rolling tray from ¾-inch plywood cut slightly larger than the
base of your sewing machine. Purchase four small wheels and attach them
to the sides of the tray so they project down below the bottom of the tray.
Attach the wheels with screws.
--
PLYWOOD BASE: Measure the width and height of the bay that will house the
sewing table, then subtract 1/8 inch from the width and Y4 inch from the
height. Using these dimensions, cut the table from ¾” cabinet-grade plywood
that matches the material from which the case is made.
Cut 3½-inch-wide cutouts to accommodate the legs. The length of these cutouts
depends on the length of the legs, which depends on the height you have
calculated for the work surface, Using the same 3 plywood, or matching 1x4
solid wood stock, make the legs to fit in the notches.
Cut a piece of cabinet-grade plywood for the storage shelf inside the cabinet.
Cut the plywood ¾-inch narrower than the width of the case because, when
folded up, the worktable lies flush with the front face of the case. Note
also that any shelves above the storage shelf that will be covered by the
worktable when it is folded up should be ¾-inch narrower than the case.
If you intend to install the rolling tray, now is the time to lay out and
rout ¼-inch (or the width of the wheels) grooves in both the table and the
storage shelf. Also cut 3 dado grooves in the sides of the cabinet at the
height of the storage shelf.
ASSEMBLY: Before assembly, check that pieces fit, then sand and finish
them to match the cabinet. Fasten the legs to the worktable using a pair
of 3½-inch butt hinges. Install the storage shelf in the cabinet, gluing
and nailing it in the dadoes.
Attach the fold-up worktable to the storage shelf by screwing one flange
of a piano hinge, cut to the full length of the shelf, to the back edge
of the worktable, then to the front edge of the shelf.
With the table flat, position the legs vertically. Hold an open, locking
brace at a 45-degree angle to mark the screw locations on the edges of the
table and legs. Drill pilot holes and install the braces. For a more finished
appearance, mark the position of the locking braces with the legs folded
up, then remove the legs and braces and rout a mortise channel in the edge
of each leg for the brace. Then reinstall the braces.
Apply veneer tape to all the exposed plywood edges. Sand and finish to
match the rest of the unit. Install barrel-bolt or other more attractive
latches of your choice to secure each leg and the worktable in place when
it is in the up position.
ADDING SHELVES AND DOORS: If you’ve installed the fold-down table in a
premade cabinet with adjustable shelves, you may have to rip a portion off
the shelves above the fold-down worktable so it will close in a flush position.
If you are building your own cabinet, plan ahead by using adjustable shelf
supports on the sides of the cabinet (or drill a series of evenly spaced
holes for shelf pins) so the shelves will be movable.
You easily can add doors to the shelf sections at the top and bottom of
the cabinet (see illustration). You can also attach prefabricated sliding
door track to the front of the shelf edges. Then cut doors from ¼-inch plywood
that matches the rest of the unit. The bottom prefabricated track should
be shallow, 1/8 - 1/16-inch. The top track should be deep enough to allow
clearance for the door panels to be lifted into place. Prefabricated tracks
are available in wood, plastic, and metal versions. In this case, however,
the tracks stick above the wood surface and may catch items that you move
in and out of the shelves.
Alternatively, you can rout grooves into the shelves before you install
them in the book case. This requires a little more woodworking skill to
make sure the grooves align in the lower and upper shelves. Cut doors out
of the same 3 cabinet-grade plywood stock, finish them to match the unit,
and install them with your choice of hinges.
MATERIALS LIST |
Item |
Material |
Length |
Qty |
Sides
Top
Bottom
Back
Upper shelf
Machine shelf
Adj. shelves
Work surface
Legs
Movable tray
Door tracks
Sliding doors
Sliding doors |
¾” plywood
¾” plywood
¾” plywood
¼” plywood
¾” plywood
¾” plywood
¾” plywood
¾” plywood
¾” plywood
¾” plywood
oak
¼” plywood
¼” plywood |
12x68
12x35
12x35
35¼x77¼
12x35”
11¾x35
8x35”
34
3½x26”
8 16”
¾”x1½”x34½”
18x10”
18x22” |
2
1
1
1
1
1
2
1
2
1
4
2
2 |
screws and nails as needed;
four casters; one 1½x34” brass piano hinge; two 1½x3½ butt hinges;
two locking folding braces; three latches; veneer tape; white carpenter’s
glue; wood putty; paint, stain, or varnish as needed |
... |