How to find and straighten the grain of woven and knit yardage.
If the fabric you’re planning to sew with was woven or knit, it has grainlines.
And if you want your project to turn out as well as possible, the first thing
you need to do with that fabric is make sure the grains are straight. Checking
the grain of new fabric as soon as you get it home gives you the choice of
returning it at once if it’s flawed, or correcting it before you sew with
it. Here’s how to tell your fabric is off grain, and what to do about it
if you still want to use it. The drawing on the facing page shows how to
locate the various grainlines, and describes how they differ. Let’s consider
woven fabrics first; I’ll come back to knits later.
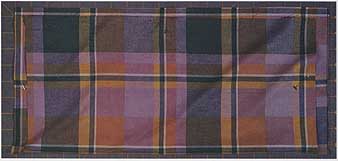
Every sewing project should start out with a layout like this:
The woven yardage has been pinned in half, with selvages and cross grain
ends together. If you see wrinkles at the fold, like those you can see here,
your fabric is off grain. Read on for your options.
Why grain is important
The significance of grain is as simple and fundamental as gravity. If you
want your garment to hang smoothly, with out wrinkles and distortion, it
must be cut so that one of the grainlines hangs vertically, plumb with the
center front, the center back, and with the center of the sleeves. In most
garments, this vertical grainline is the fabric’s lengthwise grain. Garments
are sometimes cut with the crosswise grain plumb with the centers to take
advantage of a crosswise pattern or do sign on the fabric. Of course, some
garments are cut with the centers on bias, but hat’s another topic.
In woven fabrics, either grain can work as long as you position it precisely
when cut ting to parallel the garment centers (and thus the pull of gravity), and as long as the lengthwise and crosswise grains are at exactly right angles
to one another to begin with. Cutting exactly on a grainline depends on accuracy
when laying out your pattern pieces. To make sure the grainlines are square
to each other you may have to manipulate the fabric before cut ting. This
is what “straightening the grain” means. Both steps are critical for grain-
straight garments.
How fabric gets off grain
When fabric comes from the loom, the crosswise, or weft, threads are at
exactly 90 degrees to the lengthwise, or warp, threads. In other words, it’s
grain perfect. But before it gets to the fabric store, all commercial yardage
has been rolled back and forth from bolt to bolt for processes such as -finishing,
printing, and cutting. Each time it’s rolled, it stands a chance of being
pulled off grain.
If the fabric has a permanent finish applied to it after being pulled off
grain, the grains will be permanently locked in the off-grain position, and can't be straightened. Permanent finish designations include “permanent
press,” “durable press,” “crease resistant,” “stain resistant,” “water repellent,” and “bond ed.” A permanent finish will usually be noted on the end of the
bolt. Temporary finishes, which may be labeled “pre shrunk,” “shrink resistant,”
“Sanforized,” or “flame retardant,” will wash off and won’t affect the grain.
How to check the grain
The best way to check the grain of a woven fabric is to lay the edges together,
selvage to selvage and crossgrain to crossgrain, and see if the fabric lies
flat. To make sure you’ve got the crossgrain, you can pull a thread on one
end of the yardage and cut along it or tear the fabric from selvage to selvage.
If the fabric has a crosswise woven-in stripe, you can cut along the edge
of that stripe. Printed stripes can’t be used to verify grain, since the
design could easily have been printed when the fabric was off grain. For
this initial checking, it’s only necessary to establish the cross- grain
on one end.
Pin the crossgrain line to itself on the straightened end. Place the yardage
on a flat, smooth surface, and pin the selvage edges together. Ideally, your
working surface will have a grid pattern on it so you can use it to check
straight edges.
If the yardage lies smoothly on the board with no ripples along the folded
edge, the grainlines are straight, and you can now preshrink it. Most fabric
will be in this category. But if the fabric has ripples along the fold line,
like those in the photo on the facing page, the crossgrain isn't at right
angles to the length wise grain, and you should straighten it, if possible,
be fore proceeding.
I straighten every length of woven yardage I buy, unless it’s so loosely
woven or light weight that the grain shifts just from handling it, as with
some chiffons. With these fabrics, you should establish the crossgrain at
each end as usual, but you can often correct the grain as you lay the fabric
out for cutting, holding it in place with weights, especially if your cutting
surface has a straight reference. Sometimes you’ll discover that the crossgrain
is curved. It’s usually possible to correct this kind of distortion by adjusting
the fabric as it lies flat, and steaming it.
Straightening the grain
If your fabric needs straightening, first unpin and unfold it, then trim
the other end along the crossgrain, so you can check both ends after straightening.
To return the crossgrain to its original position, simply pull on the bias
in the opposite direction of the distortion, as shown in the right drawing
above. Start in one corner, grab the selvage in one hand and the raw edge
in the other, and stretch them apart on the bias, then move your grip on
both edges down a few inches and stretch again. Repeat across the entire
length of the fabric.
Obviously, this stretching can be a challenge with wide or heavy fabric, and you may need a helper, or a bit of ingenuity. I’ll sometimes step on
one edge to hold it as I pull with both hands on the other. After pulling
across the whole thing, realign the edges to check your progress; you may
need to do it again or even to stretch a bit in the opposite direction, if
you’ve overdone it. If the fabric seems difficult to straighten, try steaming
or dampening it first.
Once the fabric is straight, with no ripples along the fold line and both
grainlines parallel with the lines on the board, re-pin the edges and steam
the entire piece. Let the fabric re lax flat for at least eight hours. Occasionally
a permanent finish will not be reported on the bolt end. If that’s the case
with your fabric, it will return to its crooked state as it relaxes, and it will be impossible to straighten.
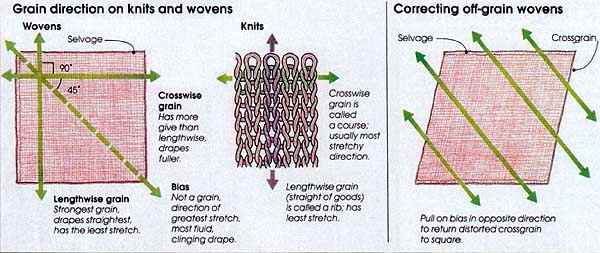
Grain direction on knits and wovens: Wovens; Crosswise
grain: Has more give than lengthwise, drapes fuller; Lengthwise grain: Strongest
grain, drapes straightest, has the least stretch; Bias: Not a grain, direction
of greatest stretch, most fluid, clinging drape; Knits: Crosswise grain is
called a course; usually most stretchy direction; Lengthwise grain (straight
of goods) is called a rib; has least stretch. Correcting off-grain
wovens: Pull on bias in opposite direction to return distorted cross
grain to square.
Last resorts
So what can you do if you can’t straighten the fabric? Return the fabric
to the store, or use it knowing the cross- grain lines are not straight.
If you cut the garment so the centers are parallel to the lengthwise grain,
ignoring the crossgrains, the garment will hang straight, but any visible
crossgrain design line will be distorted and will be impossible to match
at seams. If the fabric is plain or patterned only lengthwise, you may never
notice the imperfection. To cut the off-grain fabric, release the crossgrain
ends and pin just the selvages together so there are no ripples along the
fold line. After the fabric is preshrunk, cut it as pinned. If you had planned
to use the fabric on the bias, return it, because the bias direction only
works with grain- straight yardage.
Preshrinking
I never cut a woven or knit garment without preshrinking the fabric. Even
if the fabric doesn’t shrink, it will of ten handle more easily after preshrinking, and if it doesn’t launder or clean well, I want to know that before I put
a lot of time into it. Hand or machine baste the ends and selvages together
to preserve the grain during preshrinking.
However you plan to clean the garment, put the uncut fabric through the
same complete process, to avoid an unpleasant surprise the first time you
clean the garment. In other words, wash washables with soap, and dry-clean
dry-cleanables, don’t just have them steamed. Wetting from the cleaning fluids
can cause additional shrinkage.
I’ve used the tailors’ method of shrinking woolens, called London shrinking,
which means wrapping the yardage in a damp sheet until it’s moist, letting
it dry, then pressing it, but I think it’s too time-consuming. I prefer to
let the cleaner do it.
Working with knits
The main difference between knits and wovens in terms of grain is that,
while cutting on the straight grain is equally important to the drape of
the knit or woven garment, the grain in a knit can't be corrected if it’s
off. In fact, knit fabric really doesn’t have a grain as we know it in wovens.
All you can do is locate the straight of goods and make sure you’re cutting
on it. The straight of goods of a knit is the wale or rib running in the
lengthwise direction. The crosswise element of knit fabric is called the
course. Rolling the fabric from bolt to bolt can also distort knits, and if finishing is applied when the fabric is distorted, the distortion could
be permanent, so check the relation ship of the ribs and courses in the store,
especially if there’s a crosswise stripe or printed design. But, as with
wovens, even badly off-grain knit yard age will hang straight if cut on the
straight of goods.
Unlike wovens, which I straighten and baste before preshrinking (so the
cleaning doesn’t add to the distortion), I establish the grain in knits only
after I’ve preshrunk them, which will relax any distortion that’s not permanent.
I baste the edges together before preshrinking so that the agitation doesn’t
distort them further. It is important to wash cotton knits twice to preshrink.
After cleaning or washing, release the bastings, then locate a ribline by
pinching the fabric, folding it until a rib is parallel to the fold. Move
your fingers along the ribline, pinning at right angles every 4 to 6 in.
Work from the center to each end.
If the layout calls for a single fold and a double layer throughout, pin
the ribline at the fold, usually along the center. If you need a single layer
of fabric, replace the pins with a thread-tracing through a single layer
of the knit along the pinned ribline. If the layout calls for several different
folds, pin a ribline the length needed for each fold as you cut out the pieces.
Gently shake the knit fabric and flip it onto the cutting surface as you
would a sheet on a bed to smooth the fabric, then align the pinned ribline
with a straight line on the board. If the edges of the fabric want to roll,
spray-starch them.
When you’ve prepared your woven and knit fabric properly ahead of time,
your garments won’t hang crooked on your body, or shrink when cleaned. And
best of all, when you have a burning desire to sew, you can begin your new
project at once.
Choosing a grain board
Whatever tabletop surface you choose for your sewing workspace, make sure
it has an overall grid so you’ve got a clear, reliable, and ever-ready reference
for straight lines. You’ll find this useful in many ways, but especially
during the grain- straightening process, as described in this article. Even
those folding cardboard cutting boards can be useful. They’re pinnable and easily stored. But if you can leave your area sot up permanently, I’d recommend
either buying a table-sized, gridded rotary cutting mat, or, if you prefer
a padded surface, making one with a checked fabric top.
If you choose the mat, provide yourself with a lot of inexpensive, small
weights, so you can use them liberally, since you can’t pin into the mat.
I have a large collection of heavy metal nuts (as in “nuts and bolts”), each
about an inch wide, which I typically space about 4 to 6 in. apart around
paper patterns and the edges of unruly fabric. Even if you don’t use the
cutters, these mats make good working surfaces. There are several sources
for inexpensive gridded mats that will cover up to a 4- by 8-ft. table, and can be easily trimmed to smaller sizes.
If you’d like a padded, pressable surface, cover a sheet of ¾-in, exterior
plywood (I used a full 4- by 8-ft. sheet supported on a pair of saw horses)
with a couple of layers of wool blanket, or with nylon spring-back flannel,
the padding used by dry cleaners on their presses, available from tailors’ and cleaners’ suppliers. You can also contact Covers, Etc. For the top, I
used a woven-check cotton tablecloth, since it's more substantial than gingham.
Staple it carefully to the underside of the board, making sure the stripes
are straight and square to one another as you stretch the fabric over the
padding.
|