Not all basements can be converted to living
space, and not every one that can is worth the expense or effort. If
for instance the basement is skimpy on headroom, the solution (lowering
the floor level) may require unrealistic effort and expense. Similarly,
if water problems can’t be controlled despite your best efforts, the
basement can’t be turned into a comfortable and healthy living space.
Spend some time getting to know the basement before jumping into a remodeling
job. Common Types of Basement Walls The type of walls found in the basement, and the condition of these walls,
has a lot to do with how easy or difficult the basement is to remodel. Basement
walls are the inside surfaces of the foundation. They might
be made of concrete block, poured concrete, stone, or pressure-treated wood.
Though some are easier to work with than others, none of the foundation types
automatically prevents you from remodeling the basement. It’s easy, for instance,
to install drywall or paneling on the walls of a pressure-treated wood foundation.
(The procedure is the same used for installing it on wood-framed walls.) On
the other hand, a stone foundation sometimes has water problems that are difficult
to remedy due to the irregular nature of the materials. Walls of concrete block
or poured concrete are the most common.
Concrete Block Walls -- A foundation that’s made with concrete
blocks is easy to identify because of the grid pattern that’s created by horizontal and vertical mortar joints. Each block has a hollow core and the inside and outside faces of the block are connected by integral webs. The hollow structure
of the block makes it lighter (and easier to work with) and allows the wall
to be strengthened with the addition of reinforcing bar (called rebar) mortared
into the cores. Most blocks are identified by their nominal dimension because
that’s the measurement used to calculate how many blocks are needed in a wall.
Nominal 8” x 8” x 16” blocks normally used in residential construction actually
measure 7 5/8” x 7 5/8” x 15 5/8”. That extra inch allows for the mortar joints.
Blocks (known in the building trades as concrete masonry units, or CMU5) are
stacked one atop the other. Mortar placed between each row and each block bonds
the units and results in a strong, solid wall. Because of this construction
method, the ultimate strength and water-resistance of the basement wall depends
not just on the condition of the blocks but on the condition of the mortar
as well.
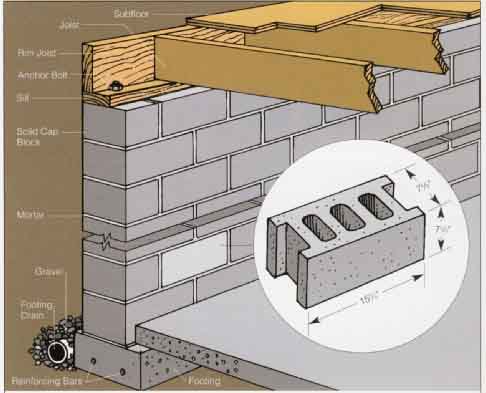
Fig. The system shown is comprised of indiv. blocks bonded together with
mortar. The blocks in the figure are the types most frequently used in residential
construction.
Poured Concrete Walls -- A poured concrete wall is monolithic and has a smooth surface, to build such a wall, concrete (a mixture of sand,
gravel, water, and portland cement) is poured into metal or plywood formwork.
Steel reinforcing bars are often placed in the forms prior to the pour. The
bars strengthen a concrete wall and help resist cracking.
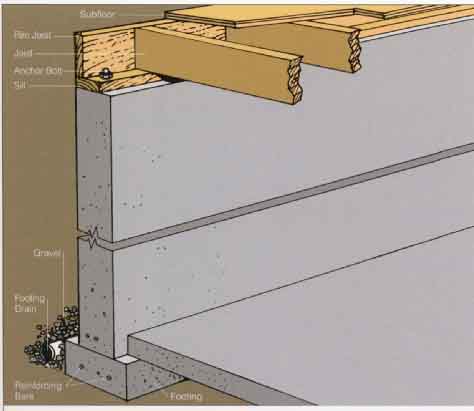
Fig. This type of wall is poured from footing to top. Steel reinforcing bars
are added for additional strength.
Other Types of Walls -- In some areas of the U.S., especially
the Midwest, builders may frame a house on top of a foundation of 2 x 8 or
larger studs and plates that have been pressure-treated with chemicals to resist
decay. This is a relatively new type of foundation. Sheathed on the outside
with pres sure-treated plywood and detailed carefully to eliminate water infiltration,
the foundation can be insulated and finished like a standard framed wall.
Stone foundations still can be found in areas of the U.S., such as the Northeast,
where some houses predate the availability of concrete. Though the type of
stone normally varies according to that which was available locally, the foundation
was usually laid up with mortar. To find out whether the foundation is in good
condition, it’s well worth having a mason inspect it before remodeling the
basement.
Looking for Trouble
Before beginning work, there is more you must know about your basement. It’s
easier to deal with an insurmountable problem before a small mountain of building
materials is delivered to the front yard rather than after.
Foundation Cracks -- Figuring out what to do about foundation
cracks is more art than science. Small hair line cracks in a concrete wall
are sometimes the fault of improper curing. Larger cracks in a foundation wall
usually are due to settling. Both types can be repaired with hydraulic
cementif the crack isn’t an active one. In other words, the crack
is patched easily if what ever caused it in the first place is no longer a
problem. If the foundation is in the process of settling, however, or if some
other factor is stressing the foundation, cracks that are patched today may
open again tomorrow. Before the cracks can be fixed permanently, the problem
has to be eliminated. To determine whether a crack is active, draw lines across
it in several places. Then check for evidence of movement over the course of
several seasons.
Inadequate Headroom -- According to building codes, a room
in the basement must have a minimum ceiling height of 90” over at least one
half of the room. The only exceptions are bathrooms, kitchens, and hallways
which are allowed a ceiling height of 84”. Minimum headroom measurements are
taken from finished surfaces. If a measurement between the basement floor and the underside of the joists does not meet these standards, t may be impossible
to get a permit.
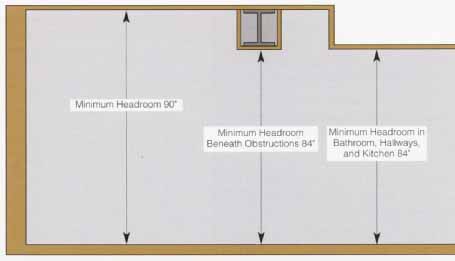
Fig. Building codes allow less headroom in bathrooms, kitchens, and hallways
than in other living areas.
Poor or Inconvenient Access -- Getting into the basement
usually isn’t a problem. The stair might have to be repaired, but at least
it already exists. When it comes to basement bedrooms, however, having an exit
in case of an emergency also becomes an issue. According to code, all bed rooms
in the basement must have a means of emergency exit. A door that leads directly
outside from a bedroom (and not to a bulkhead door) qualifies
as an emergency exit. If no such door exists, there must be a window that can
be used instead. The requirements for such a window (called an egress window)
is 5 sq. ft. of open-able area. If your remodeling plans include a bedroom,
make the egress issue the first order of business.
Inadequate Air Circulation -- All rooms become uncomfortably
stuffy when the air in the room isn’t renewed with fresh air periodically.
Building codes call for operable windows equal in size to at least four percent
of the room’s floor space. (Don’t confuse this figure with the amount of glazing
needed to provide natural daylight in a basement)
In a basement, however, this isn’t an easy percentage to achieve, so the codes
offer the following exception: If a room is served by an “approved” mechanical
ventilation system that’s capable of changing the air every 30 minutes, operable
windows are not required. An “approval” must be given by your local code officials,
however, so check with them before deciding to pursue this exemption.
Humidity, Dampness and Moisture Problems -- Of all the possible
roadblocks to making the basement livable, moisture problems can be the hardest
to solve. Water is incredibly persistent, and under the right circumstances
can make its way through walls that are considered impermeable. Another source
of moisture is the condensation that forms as warm, moist air reaches the cold
surface of a masonry wall. Some moisture problems can be remedied. However,
major problems may call for professional assistance and considerable expense.
An easy test for water problems is done by taping pieces of aluminum foil
to various places on the walls and floor. Seal the edges tightly, and leave
the test patches in place for several days. If moisture droplets appear beneath
the foil after several days, moisture is migrating through the masonry; if
they appear on top of the foil, the problem is condensation.
When looking for water problems, investigate the underside of the floor sheathing
for signs of leaks. Now is the time to fix faulty pipes and fixtures. Inspect
the sheathing and the sides of the joists for brownish stains which may indicate
an active leak or an old leak that has since been repaired. If the stain is
spongy when probed with a flat-blade screwdriver, an active leak exists somewhere.
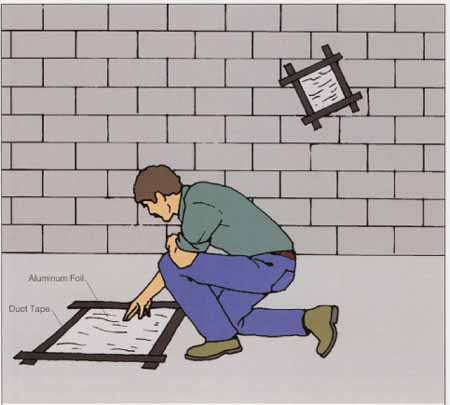
Fig. Tape a patch of aluminum foil to several sections of the floor and walls.
If moisture droplets collect underneath or on top of the foil, a moisture problem
exists and must be corrected.
Problems with “Bugs” -- The floor system of most houses rests
on wood “plates” that are bolted to the foundation. If the house has a problem
with wood- destroying insects, this is where the evidence will be found. Check
the outer foot or so of the floor joists, the inside surface of the rim joist, and the wood frame of every basement window. Keep an eye out for signs of powder-post
beetles, carpenter ants, and non-subterranean termites. Signs of insect problems
include swarming insects, a series of pinholes in the wood, and small powdery
piles of sawdust beneath affected wood. If things look suspicious rap the wood
with your knuckles—infested wood sounds different than solid wood. To search
for rot or insect damage, use the tip of a scratch awl to poke at the rim joist,
the plate, the ends of the joists, and window framing (even if it looks sound).
Rotten or bug-infested wood yields easily. (Building inspectors have been known
to use a ski pole with a sharpened tip to poke at the rim joists, eliminating
the need for a ladder.) Infested areas must be treated by a professional exterminator
before remodeling work can begin.
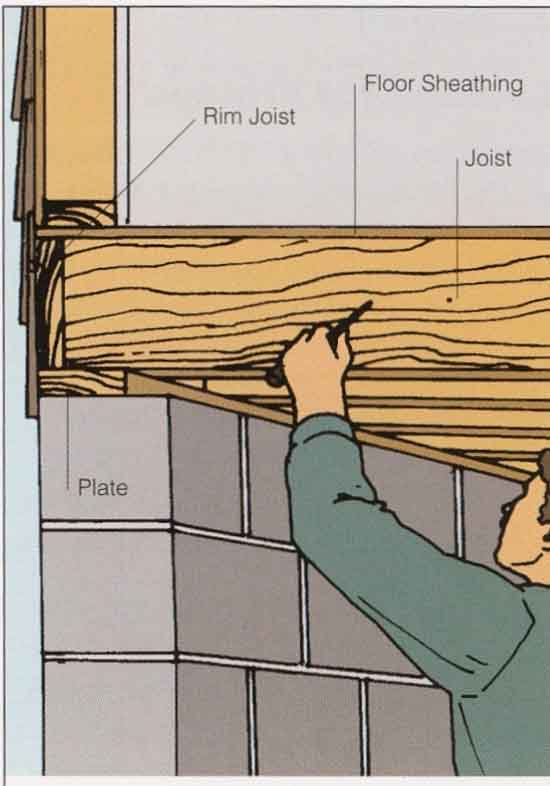
Fig. Use an awl to investigate the rim joist area. Rotten or bug-infested
wood yields easily.
Sagging Joists -- Sight across the underside of the floor
joists to better see whether they are out of line. Those that are out of line
are probably damaged but most likely can be repaired easily. If all the joists
sag noticeably, however, it may be that they are improperly supported or undersized.
In either case, a remedy is readily available.
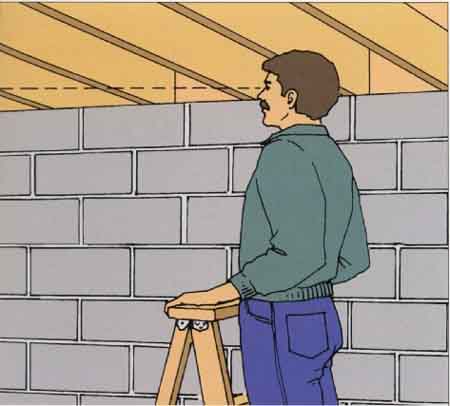
Fig . Sight across the underside of the joists to spot those that are out of
line. Then check to see whether the whole floor system is sagging. |