Properly planned and completed in stages, even a major renovation can
be minimally disruptive, so that you will still have a place to store dishes,
to cook, and to serve meals. Large upgrades cost more than $7,000, although
many can be completed in a day or two.
Installing Hardwood Flooring
The first question a prospective client asks about a hardwood floor is,
“Is it hard to clean?”
Bumpy, grooved, plugged, and notched hardwood flooring not practical for
the kitchen. Although it may look good in the showroom, it doesn’t hold
up well to moisture and food spills. Use a square-edged, flush-jointed
style in the kitchen, and take special care to ensure tight joints between
planks on all four sides.
There are two types of pre-finished hardwood flooring—solid planks and veneered plywood planks. The latter are highly susceptible to damage from
falling objects and once damaged are nearly impossible to repair. Solid
planks resist most kinds of abuse and can be refinished again and again.
Solid-plank hardwood costs 30 to 50 percent more than veneered plywood
planks but will last 10 times longer.
For lasting quality, take two precautions when installing hardwood. First,
always use a vapor barrier between the subfloor and the hardwood flooring
boards. Second, never glue the hardwood directly to the subfloor. The correct
way to attach prefinished hardwood floors is to nail a layer of underlayment
to the subfloor and then glue the hardwood to the underlayment.
The finest hardwood floor is the custom floor. It is nailed directly to
the subfloor over a moisture barrier, then it's put tied, sanded, stained, and varnished in place. This type of hardwood floor is the most water-resistant and easiest to clean. Even though it's the most expensive, it's also
the longest lasting, which makes it the most cost-effective type of flooring.
Installing Expensive Countertops
Expensive countertop materials, such as Corian and slab marble and granite,
can be stunning additions to a kitchen. Their durability and ease of maintenance
complement their exceptional beauty.
Corian is a popular synthetic countertop material that's durable and stain resistant; in addition, accidental cuts can be repaired by sanding.
Corian and similar synthetic products are popular in finer homes; they
cost approximately 35 percent more than ceramic tile and about five times
as much as plastic laminate. For an interesting look, trim synthetic countertops
with a ceramic tile back splash, and use wood or metal trim for an unusual
edge detail.
Synthetic slab countertops made of cultured marble, cultured onyx, and cultured granite are better used in bathrooms than in the kitchen, since
they are easily stained by food and beverages and are less durable than
Corian and similar synthetics.
Natural slab granite is durable, beautiful, unique, and expensive. A granite
countertop will not provide much of a return in a first-time-buyer’s neighborhood,
but it can be considered a sensible investment in move-up homes.
Granite is available in a wide range of prices, depending upon the type
used and how it will be edged. Some types are more widely avail able than
others, making them less expensive. The slabs are usually ¾ inch thick
but are made to look thicker by having a second piece glued onto the underside
of the front edge. Polishing can make the seam almost invisible to the
naked eye.
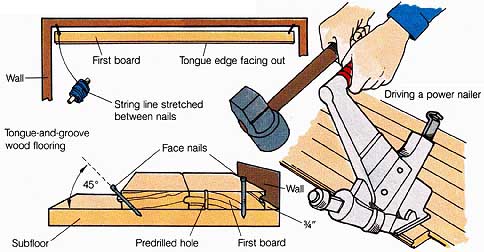
Installing Hardwood Flooring
Installing a Bow Window
Adding a bow window at the kitchen sink can turn a small, plain kitchen
into a light, airy, spacious-looking one. The project is relatively expensive,
but if a room addition is out of the question and the kitchen is cramped,
a bow window could be the most cost-effective alternative.
Bow windows differ from bay windows in that they have four or more panels.
Bay windows have three. Bow windows are available in aluminum, vinyl, wood, and clad wood frames. Cladding is available in aluminum or vinyl. It is
important to use a frame material that matches that of the rest of the
windows in the house. A wood-framed window installed in a house with aluminum
frames might look out of place and could actually diminish the value of
the home.
Installation cost is the main reason that a bow window is more expensive
than other types of specialty windows. Structural alterations are usually
necessary. This project should be planned with the help of an architect
or a designer and a contractor or an engineer.
Loss of usable wall space is a drawback to a bow window. If the bow window
is wider than the window being re placed, the opening in the wall will
have to be enlarged. Reduced wall space also might result in the loss of
wall cabinets. Consider these trade-offs carefully. You might decide to
install a skylight instead.
Installing a Skylight
A skylight can add natural light and , with some models, ventilation to
an otherwise dark and dreary work place without diminishing wall space.
A skylight itself is relatively inexpensive, but installation can involve
costly structural alterations. Plan the installation with the assistance
of a professional. This is important be cause proper installation is necessary
to reduce the chance of leaks. Skylights themselves don’t usually leak.
Most often, leaks occur at a faulty joint between the skylight and the
roof.
The installer should use connection details provided by the National Roofing
Contractors Association in its Roofing and Waterproofing Manual. The
installation information provided with the skylight may not be sufficient
to ensure a watertight configuration with every type of roofing material.
Metal flashings are usually required for the installation. Some skylight
companies offer the flashing at extra charge; if they don’t, a heating and sheet- metal contractor can make them. Some tile roofs require lead
flashing for a proper seal, which can be expensive. Roofing contractors
are expert in this area.
Do not use canned roof patching compound (a cold patch) to install a skylight
in a hot-asphalt type of roof. The connection will not last and eventually
a leak will occur. Use hot asphalt for a more permanent seal, even though it's more expensive initially.
Installing a skylight in the kitchen is somewhat different from installing
one in most other rooms, mainly because the kitchen requires more artificial
lighting in the ceiling, which leaves less space available for a skylight.
During the planning phase it's important to consider rearranging rather
than eliminating any artificial lighting.
There are two basic types of skylights—fixed and operable. A fixed skylight
(one that doesn’t open) is the least ex pensive of the two. It is avail
able with either a domed plastic lens or a flat glass lens. Of these two,
the domed plastic lens is the least expensive and most commonly used.
Operable skylights, some times called sky-windows, can be opened and come
in a wide variety of styles. Some open only on the side to improve ventilation;
others lift open. Some can be opened and closed manually; others have electrical
controls. Some electrically operated models have moisture sensors that
will close the sky light automatically in the event of wet weather. Louvered
blinds to reduce heat and light on hot days are another option; the blinds
in some models open and close electrically.
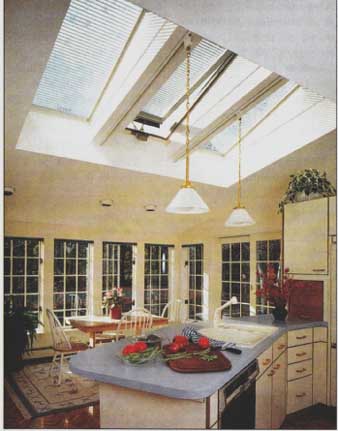
Skylights and casement windows brighten this remodeled eat-in kitchen.
Other new touches include recessed lights in the eating area, hardwood
floors, and an appliance garage.
Re-facing Cabinets
Advertisements claim that cabinet re-facing can be done for 5 percent
of the cost of replacement, and it’s true. It’s also true that a refaced
surface, done properly, will last a long time and be worth the price. How
ever, replacement, not re-facing is best if you are planning to remodel
your kitchen completely and if the existing cabinet space is arranged inefficiently.
All appliances must be re moved before re-facing can begin. Then remove
moldings, drawers, blank drawer fronts, and doors and hinges. Rough the
remaining surfaces with sandpaper (50 to 80 grit), and ply a layer of contact
cement. Also coat the back of the veneer to be used for re-facing with
contact cement. Allow the cement to dry, and then press the veneer onto
the cabinet surfaces and trim the edges with a router, razor knife, file, and sandpaper. If plastic laminate is the veneer of choice, paint the cabinet
interiors before beginning the re-facing process. Next, install new moldings,
doors, and drawer fronts. Finally, if the veneer is wood, you can either
apply stain and varnish, or paint.
A good re-facing job requires lump-free adhesive application and careful
trimming of the newly applied veneer. Grained veneers should be applied
so that the grain runs in the same direction, usually vertically, except
on horizontal rails.
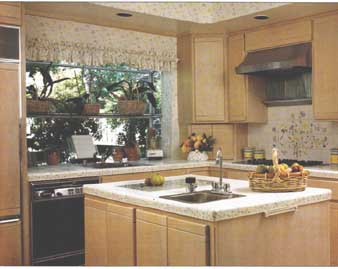
The delicate floral trim in this kitchen is repeated in the wallcovering and matching fabric, the tile back splash, and the island countertop
trim. Note the electric power strip on the island and the refrigerator
faced to match the cabinetry.
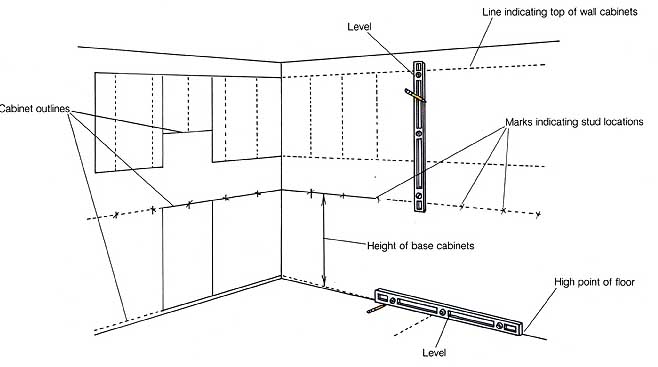
Kitchen Cabinet Layout
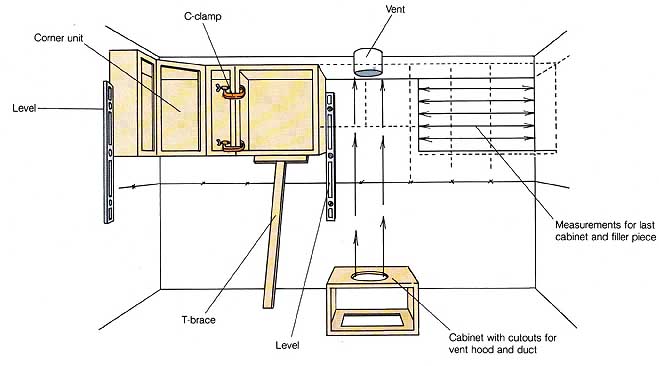
Wall Cabinet Installation: Cabinet with cutouts for vent hood and duct;
Replacing Cabinets
Cabinet replacement is most cost-effective when you are completely remodeling
the kitchen. Damage to cabinets and countertops is most likely during the
removal required for most major kitchen remodeling.
As has been noted previously, the markup on prefabricated (modular) cabinets
is high, so when shopping for modular units, expect 50 to 70 percent discounts.
This is not true for custom cabinets, al though prices will vary greatly
from cabinetmaker to cabinet maker, depending on quality of construction,
accessories, door style, and finish. Not every cabinetmaker is a good de
signer. Professional design assistance is most important to achieve a high-quality
finished product.
Dovetailed drawer construction is the finest, but its absence should not
preclude the importance of strong hard ware (drawer glides and hinges),
thick cabinet walls, finished interiors, good-quality wood products and accessories, and a fine finish.
Factory-applied varnishes ire usually superior to those on locally made
cabinets. However, cabinets with “photo-finished” surfaces, such as contact
paper, are not a good investment.
Adding Island Cabinets
Island cabinets can make a kitchen more versatile and in nesting. It is
important when installing them to avoid creating tight passageways. To
find out how well an island cabinet would work in an existing kitchen,
try the following. Measure a point 3 feet in front of the dishwasher and place a kitchen chair on the mark. Open the dishwasher, bend over, and pull out the bottom tray. If your body doesn’t bump the chair, you have
enough space to install an island. Perform this experiment with any appliances
that will open into a walkway created by the installation of an island
cabinet.
Remodeling or Expanding a Kitchen
Statistics show that you can expect a 75 to 110 percent return on your
investment from a kitchen remodeling project, with expansions returning
slightly less. This excellent re turn compounds the pleasure of having
a safe, luxurious, modern work center.
No home improvement is more satisfying than a complete renovation. But
the process can be stressful. You can minimize the stress by making as
many decisions as possible before the project begins, pre paring a separate
cooking and sink area to be used during construction, and accepting that
your life will be in disarray for many weeks.
The success of a kitchen remodeling project or expansion depends on planning.
Every detail must be thoroughly studied. Making a wants and needs checklist
of every feature in the new kitchen can make planning easier. Architects,
de signers, and contractors can get a better idea about your dream kitchen
by knowing your preferences.
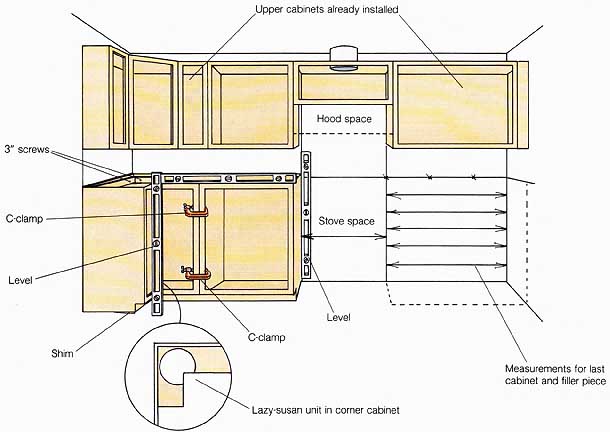
Base Cabinet Installation: Measurements for last cabinet and filler
piece; Lazy-susan unit in corner cabinet; Upper cabinets already installed.
|