Wallboard is known by many names. Whether it’s called gypsum-board, plasterboard,
drywall, or Sheetrock (a trade name), the product is the same: a solid gypsum
core covered on both sides with heavy paper. It’s an inexpensive, all-purpose
surface that can be used in any room of the house.
Installing wallboard panels is relatively simple. It’s the taping and finishing
that require patience and practice. Before you decide to do it yourself,
consider hiring professionals to handle the job. This is especially true
if you dislike projects requiring careful attention to detail. As a rule
of thumb, if more than three panels or 100 square feet are involved, get
estimates first. The total cost of a professional job may compare favorably
with your material costs alone.
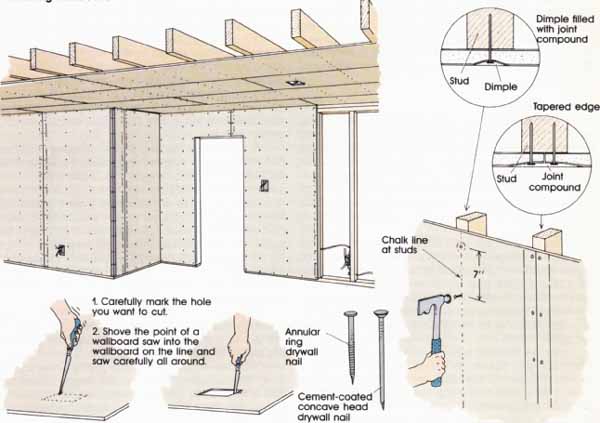
Installing Wallboard: 1, Carefully mark the hole you
want to cut. 2. Shove the point of a wallboard saw into the wallboard
on the line and saw carefully all around.
Planning
Begin by planning the installation on paper. Work out a pattern that results
in the fewest number of joints. Al though minimizing waste is always a concern,
in this case minimizing your labor is even more important. Wallboard is
so inexpensive that you should use full sheets whenever you can. It’s not
worth bothering with small pieces just to save a few dollars.
The long edges of wallboard panels are tapered slightly to accommodate
several coats of joint com pound; the 4-foot edges aren't . So plan to join
panels along the long, beveled edge whenever possible. When end joints can’t
be avoided, stagger them so they’ll be less noticeable.
Longer panels, such as 4 by 12s or even 4 by los, make it possible to span
the entire length of most walls. Planning joints to fall above and below
windows and above doors also means less taping. For ceilings, use panels
that span the longest distance, providing they run perpendicular to the
joists. The longer lengths are heavier and harder to install, but you’ll
save time because less finishing is required.
Preparing Studs and Joists
Before any panels are applied, prepare the studs and joists. Pull any nails and scrape away small pieces of old wallboard or paneling. If you are replacing
lath and plaster, the new wallboard probably isn’t the same thickness as
the old surface. In order to make the trim around doors and windows lie
properly, use any of the following techniques that apply.
• Add matching wood strips behind the trim to fill the gaps. This takes
time but is practical if there isn’t much trim. If the gaps are small, you
may be able to fill them with caulking after the wallboard is installed.
• Use two layers of wallboard. This solution is generally too expensive
to be feasible, although it does provide extra soundproofing.
• Shim the studs with old lath or any suitable stock that creates the proper
depth. For example, to replace 3 plaster with 1/2-inch wallboard, shim the
studs with 1/4- by 1 ½-inch lath. Tack the lath in place along the length
of each stud. When the panels are applied, use a longer nail that drives
through both wallboard and lath into the stud.
• Check the studs with a plumb bob to see if they are reasonably plumb.
As long as the wall is a smooth plane, slight irregularities won’t be noticed.
Use shim stock to correct obvious problems.
• Check the wall and ceiling surfaces to see if they are square. Measure
the diagonals of the surface. If the dimensions disagree by more than 1/2
inch, you may need to trim one or more panels along the edge to fit. Or
you can try compensating slightly as each panel goes up. Otherwise you’ll
come to a panel that falls off the edge of a stud or joist.
• Check the wall and ceiling for sufficient nailing surfaces. Wallboard
panels should not be applied with unsupported edges. If a corner or ceiling
line needs a nailing surface, nail in lengths of 1 by 2s or 2 by 4s as needed.
If only part of the surface is to be replaced, and the old wallboard is
cut next to a stud, nail a 1 by 2 along the stud to serve as a nailer for
the new panel.
• Check where any wires or pipes go through the studs or joists. They should
be at least 1 1/4 inches back from the edge, or protected by metal stud
guards.
• Finally evaluate whether any of the walls needs additional shear strength.
Adding shear strength usually involves glue nailing 1 or 3 plywood to the
studs before wallboard is applied. Your building department or a qualified
engineer can advise you and recommend a nailing pattern for the plywood
panels. If you have to strip some walls anyway; adding shear panels in the
right places is a very cheap way to substantially strengthen your home.
Cutting Panels
When cutting panels, use a guide such as a 4-foot-long wallboard T-square
or a straightedge. Any long, straight piece of wood will do. The panel can
be leaning against the wall or lying flat on the floor. With a sharp utility
knife, cut through the face paper and score the gypsum core. Use several
light strokes rather than bearing down on the knife. Then apply firm, even
pressure to snap along the cut. Fold the cut portion back and slit the paper
on the other side.
To cut an opening, first measure carefully. Then double check it. Remember
which surface is the front and always measure from the top down. A technique that's sometimes helpful is to cover the edges of electrical boxes with
chalk. Then transfer the chalk to the wall board by pressing the panel against
the wall. However, be sure to keep cuts on the front of the panel smooth,
with no ripped paper.
Once the opening is marked, cut the sides with the utility knife and punch
out with a hammer. Or, using a pointed wallboard saw, start the cut by plunging
it through the panels well within the outline. For right angles mark the
opening with a pencil and cut the shorter leg with a wallboard saw. Then
cut and snap the remaining leg with the utility knife. For U-shaped openings
first cut the two opposite legs with a saw and then cut and snap the remaining
side with the knife.
Cut edges will often be slightly uneven. Don’t waste time planing or chipping
them smooth. Cut the panels 1/4 inch short in the first place. The jagged
edges will fit together more easily, and the gap can be filled later with
joint compound. Without enough clearance, at tempts to force the panel in
place will usually break the core and spoil the edge.
Applying Panels
Apply the ceiling panels first. For this you need at least one helper,
maybe two. (A 4-by-8 panel 1/2 inch thick weighs about 60 pounds.) Even
with a helper, renting a wallboard jack or using two T-braces, called deadmen,
is a good idea. Make the braces from 1 by 4s or 2 by 4s. The top of the
T should be 2 to 3 feet wide, and the total length should be the floor-to-ceiling
height plus 3/4 inch. Be careful not to gouge the paper surface of the panel.
Another technique is to temporarily nail a 1 by 4 to the ceiling joist and use this as a lip for the edge of the wallboard. This carries some of the
weight while the panel is nailed in place.
Position the length of the panel perpendicular to the ceiling joists. The
edges should cover just half the width of the surrounding joists. Drive
nails through the center of the panel first and then work around the perimeter.
If you have difficulty sighting the joists, mark the panels with a pencil
or snap a chalk line as a guide. The correct nailing pattern depends on
the local building code. Check this beforehand. In many instances this is
every 7 inches on ceiling panels and every 8 inches for walls. Along the
perimeter the nails should be 3/8 to 1/2 inch from the edge. Once the nail
is flush, give it one last blow to slightly dimple the surface but not hard
enough to break the paper. This allows the nail heads to be covered with
tape and joint compound. Don’t countersink the nails or break the paper.
To cover the walls begin, with an upper corner and position the panel flush
with the ceiling. For vertical panels lift from the bottom edge with a foot
lever, which is simply two pieces of 1 by 4 or shim stock used to create
a fulcrum. If you’re applying the panels horizontally, have a helper support
some of the weight. Several nails or a wood block nailed beneath the lower
edge of the panel can also serve as temporary supports.
Be sure the leading edge of the panel is vertical and covers just half
the width of the last stud. If the corner isn’t square, you can leave a
gap of up to 1/2 inch, which can be covered with tape and joint compound.
If the studs are new wood, use two nails 2 inches apart spaced every 12
inches, instead of a single nail every 7 or 8 inches. This will minimize
the chance of popped nails in the future.
Once the wall panels are in place, cover any out side corners with metal
corner beads. Drive nails through the bead into the framing about every
5 or 6 inches. The nail heads and bead will be covered with joint compound.
Taping and Finishing
To cover the joints and nail heads, use the ready-mix joint compound that
comes in gallon or 5-gallon containers. Use a separate container or mortarboard
while applying the compound. Otherwise dried pieces will work their way
into the fresh compound and make the job more difficult. In total you will
put down three separate layers (each about 1/16-inch thick), gradually build
lug the surface each time. Keep in mind that smooth, neat work at each stage
is rewarded with less work in the long run and a better-looking finish job.
Using a 6-inch knife, cover all the nail holes in the center of the panels
with joint compound. Next fill the gap between panels and spread a thin
layer about 4 or 5 inches wide over the joint. Use your fingers or your
knife to press a section of paper tape into the wet com pound. Although
the most efficient technique is to unroll the tape with one hand and use
the other to smooth the tape with the knife, this takes practice. Feather
out the edges and add a small amount of compound over the top of the paper.
Be sure to eliminate any wrinkles or air bubbles. For inside corners apply
compound to both sides. Then fold the paper in hall, press into the corner. and smooth with the knife.
Let this first coat dry overnight. Repeat with a second coat 24 hours later,
feathering out several inches on either side of the first coat. The total
width of the joints is now 7 to 10 inches.
Use a 10-inch knife for the third and final coat. The width of the joints
should be about 10 to 13 inches. For inside corners it’s often easier to
do one side at a time and let the compound dry Then come back and do the
other side.
After the compound is thoroughly dry smooth the joints and nail heads with
80- or 100-grade sandpaper wrapped around a wood block. If you’ve done a
careful job with the knives, there’s little sanding to be done. Because
the paper on the panels fuzzes easily, be sure to sand only the compound.
An alternate technique that eliminates the gypsum dust is to use a wet sponge.
This smooths the compound nicely as long as the surface isn’t allowed to
get too wet.
The next step is either painting or texturing. Texturing involves trowel
techniques best left to a professional. Painting involves priming with a
special latex sealer called PVA and finishing with a final coat or two of
the chosen color.
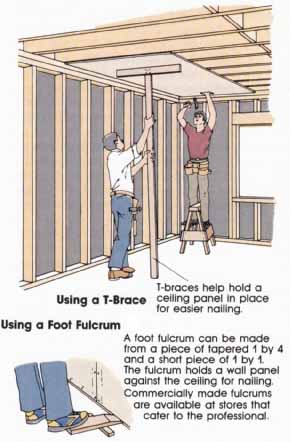
Using a T-Brace: T-braces help hold a ceiling
panel in place for easier nailing. Using a Foot Fulcrum: A foot
fulcrum can be made from a piece of tapered 1 by 4 and a short piece of
1 by 1. The fulcrum holds a wall panel against the ceiling for nailing.
Commercially made fulcrums are available at stores that cater to the professional.
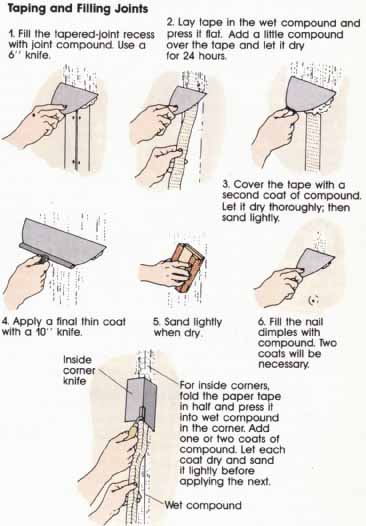
Taping and Filling Joints: 1. Fill the tapered-joint
recess with joint compound. Use a 6” knife. 2. Lay tape in the wet compound and press it flat. Add a little compound over the tape and let it dry for
24 hours. 3. Cover the tape with a second coat of compound. Let it dry thoroughly;
then sand lightly. 4. Apply a final thin coat with a 10” knife. 5. Sand
lightly when dry. 6. Fill the nail dimples with compound. Two coats will
be necessary. Inside corner knife; For inside corners, fold the paper tape
in half and press it into wet compound in the corner. Add one or two coats
of compound. Let each coat dry and sand it lightly before applying the next.
|