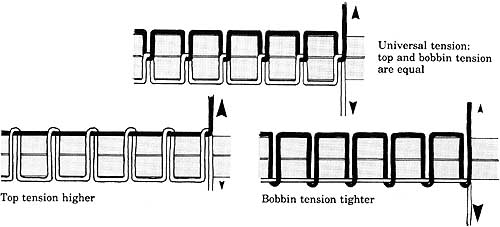
Visual Glossary: Universal tension: top and bobbin tension are equal.
Bobbin tension tighter. Top tension higher
The straight stitch is so versatile that even if you did nothing but straight-stitch
machine embroidery, you would have enough ideas and work to keep you busy
the rest of your life.
In its simplest form straight stitch looks like the drawn line, as in the
scenes on Shirley F’s vest (Fig. 2-1). Similarly, you can distort rows
of straight stitch to create pattern, as Lois E. has done in Fig. 2-2.
Straight stitch is often used to out line a shape (Fig. 2-3). It is also
used to emphasize a line with a thicker thread, like buttonhole twist in
topstitching.
How a Stitch is Formed
But before going any further, let me ask you an embarrassing question: Do
you really know how a stitch is formed on the sewing machine?
Don’t laugh — understanding how the machine works explains how it doesn’t.
And don’t be embarrassed—in a continuing private survey, I’ve discovered
that most people don't understand how a stitch is formed, even if they have
been sewing on a machine all their lives.
After examining Figs. 2-4 and 2-5, you can see that if, for example, the
fabric isn't flat against the needle plate at the moment the needle enters
the fabric, the shuttle hook on the bobbin will not catch the loop of top
thread, and therefore a stitch will be skipped. Remember this, especially
when you are doing free machine embroidery.
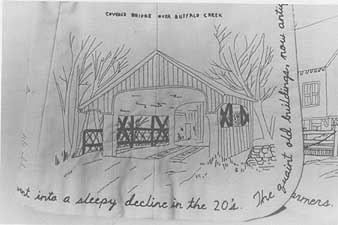
Fig. 2—1 Bottom of a vest by Shirley F. created to honor scenes of Long
Grove, IL. The covered bridge over Buffalo Creek
is worked in straight stitch with the presser foot on (white muslin with
brown thread). The lettering is by hand.
Troubleshooting Stitching Problems
Some of the other stitching bugaboos you might run into, and why they occur,
are:
1. The upper thread breaks:
a. The machine isn't threaded properly or the needle is inserted wrong
way round or at the wrong height.
b. Upper tension is too tight.
c. The thread is dry and brittle; or too thick for either the needle or
material; or knot ted somewhere between the top spool and the needle.
d. The needle is bent or blunt.
e. The presser foot isn't lowered.
f. You are taking the first stitch too fast for the thread being used (e.g.,
rayon)— start slowly.
2. The lower thread breaks:
a. Lower tension is too tight.
b. The thread is unevenly wound on the bobbin or brought up incorrectly.
c. The hole in the needle plate is old and scarred and needs a light filing
with a machinist’s file (sewing machine dealer can do this).
3. The needle breaks:
a. The material has been jerked during sewing, bending the needle and causing
it to hit the presser foot or needle plate.
b. The upper tension is too tight for the machine.
c. The needle is mounted incorrectly.
4. Stitches are uneven or skipped:
a. The bobbin innards are linty and clogged.
b. Needles being used are not made expressly for machine.
c. The needle has a scooped-out part (called a scarf) too shallow for the
thread or stitching method being used — use a Yellow Band or Stretch needle.
d. The machine is incorrectly threaded.
e. The fabric was not touching the needle plate at the moment the stitch
was formed.
5. The material puckers:
a. Thread is too thick for the material — use a stabilizer.
b. Upper and /or lower tensions are too tight.
c. Stitches are too long.
d. Fabric was jerked away from needle at end of stitching, gathering fabric,
rather than pulled gently to the side, pinching ends of threads.
e. Fabric needs added body to withstand heavy stitching (especially in zigzag
stitching) — use stabilizer.
Any other machine irregularities, such as poor timing or sluggishness, should
be checked by a dealer.
I won’t fill your ear with the details of which needle and thread to use
with which fabric. If I start listing them here, you’ll just yawn and say
“Oh, that” and you won’t learn anything at all. So right now I’ll tell you
the barest minimum and when in the future you need more specific information,
you can turn to the Needle and Thread Chart in Section 13, Know Your Tools.
Incidentally, American, Japanese, and European needles have different numbering
systems, which is why I always give two numbers—e.g., Size 14(90) means Size
14 for American machines and Size 90 for European and Japanese machines.
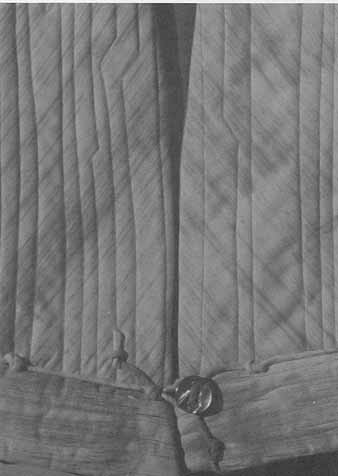
Fig. 2—2 Close-up of vest by Lois E., the author of Fabrics Reconstructed.
Straight stitch channels create counterpoint to the lines of the dyed fabric.
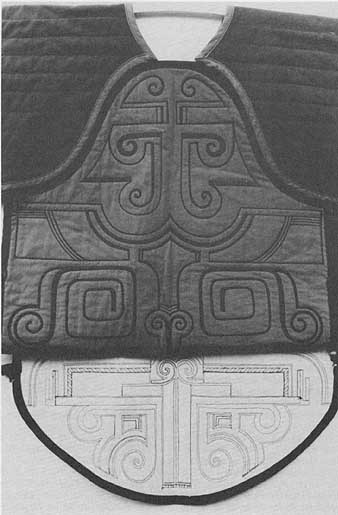
Fig. 2—3 Burgundy and pink tabard by Nancy G., quilted by lines
of straight stitch following designs drawn onto the fabric with an indelible
laundry marker. The front is folded under to show the quilting lines on
the underside of the back.
Thread
As for thread, we now have a cornucopia of choices — cotton, rayon, polyester,
silk, metallics, cotton-wrapped polyester. Since the numbering system used
for threads isn't uniform throughout the world—e.g., an American size 50
thread is thicker than a European size 50—I will avoid confusion by describing
threads as extra-fine, ordinary, and heavy, rather than by size number. See
the Supply List for brand names under each category.
I use ordinary cotton-covered polyester for garment construction, but hardly
at all for machine embroidery, as the outer fiber tends to shred, causing
the thread to knot and break. But I do use extra-fine cotton-covered polyester
for satin stitch. Since new threads are being introduced all the time, don’t
reject any thread without giving it a thorough workout. Experiment with loosening
top tension and using a larger sized needle if your thread breaks while playing
with it.
Fabric stores now carry European, Indian, Thai, and Japanese threads of
100% cotton, rayon, silk, or polyester that are extra-fine and that produce,
in particular, remarkable free-machine embroidery. Check the Supply List
for Internet and mail-order sources and ask your favorite fabric store to
stock a full range of colors.
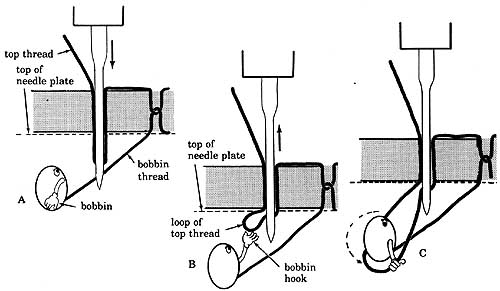
Fig. 2—4 How a stitch is formed. A. Top thread meets the bobbin. B.
A tiny loop is formed by top thread. C. Bobbin grabs the loop and locks
the stitch below the fabric.
In most cases you will use a size 12(80) or size 14(90) needle with ordinary
sewing-machine thread, but re member that you choose the thread to suit the
fabric and the needle to suit the thread. On organza, for example, you would
choose extra-fine cotton, rayon, or silk sewing-machine thread matched with
a size 10(70) needle. Remember that the purpose of the needle is to make
a hole in the fabric big enough for that diameter of thread. If the hole
isn’t big enough, the thread is cut by the edges of fabric surrounding it.
If you backed your organza with stabilizer, you are working with a heavier
fabric than plain organza alone; therefore, you may need the next larger
size of needle.
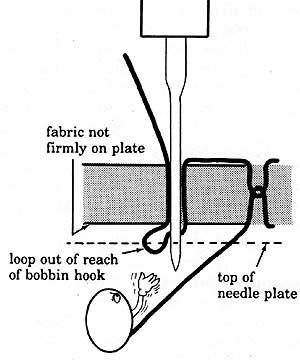
Fig. 2—5 How a stitch is skipped: If the fabric isn't flat against
the needle plate, the loop lifts out of reach of the bobbin hook and a
stitch is skipped.
Preparing Fabric / Preventing Puckering
You’re impatient to start sewing, aren’t you? But before you can do even
an inch of straight stitch, your fabric must be prepared. If your fabric
will later be washed, preshrink it now by wetting the fabric and drying it
in a hot dryer (except for permanent press fabrics—use a cool to warm dryer).
If you’re making something that will be washed, be sure your threads are
color fast (silk floss, for example, isn't guar anteed colorfast). Iron
fabrics with wrinkles.
Some fabrics will need extra body to keep the stitches from puckering the
material. Medium- and heavyweight woven fabrics may not need any help (always
make a test cloth), but the lighter weight cottons and almost all knit fabrics
need to be stiffened by a stabilizer (your choices were listed in Section
1).
Which stabilizer is best? The answer varies. When you enter the world of
the machine-embroidery sub-cult, you enter a busy, happy hive of opinionated
quirks. One person uses only paper as stabilizer and that paper must be Women’s
Wear Daily because it’s the correct weight and the ink doesn’t rub off.
“Paper!” screams another aficionado in horror. “I can’t stand that clackety,
clack sound and it dulls the needle. Only tear-away for me, thank you. And
I don’t put the stabilizer in the hoop— only the fabric.”
Use what you like and what you can afford. (Jackie Dodson says she once
found a Chinese newspaper behind em broidery on a T-shirt from Taiwan.) Most
often you will use tear-away stabilizer, which comes in light and crisp weights.
You can also use water-soluble stabilizer, which disappears when wet.
But if you run out of either, don’t despair. There are other ways to prevent
puckering. Putting a piece of typing pa per between the fabric and the needle
plate helps. The paper is then gently torn away after stitching (Fig. 2-6).
The paper trapped by the stitches disappears with the first wash.
The weight of paper you choose depends on how heavy the stitching will be,
whether or not you’re using a hoop, or whether the embroidered article will
be washed before use. Use typing- weight paper if you don’t use a hoop. Choose
tissue paper if you use a hoop and want the embroidery to have a soft feel
even if it isn’t washed. (You can al ways put the fabric in a hoop and pin
the stabilizer underneath it.) If you have a large piece of fabric to stitch
in long rows, tear the typing paper in long strips or use adding machine
tape. If you have large areas to stitch, use shelf paper. A third kind of
paper to use is plastic-coated freezer paper from the grocery store, which
is ironed onto the underside of your fabric and acts like a square hoop.
Remove it by ironing again, which loosens it, and tear it off.
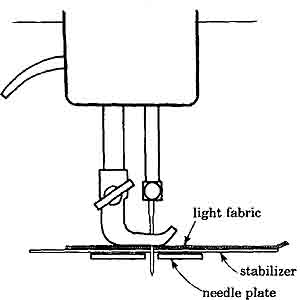
Fig. 2—6 Stiffen light fabrics with stabilizer.
Other ways to prevent puckering include spray-on starch ironed into the
fabric to give extra body for intricate stitching.
More often I back fabrics with a piece of organza, organdy, or lightweight
iron-on interfacing. You can even draw your design on the organza or interfacing and decorate the piece from the wrong side, as described in Section 1.
For all garments to be home-sewn and embroidered, be sure to do the embellishing
before you cut out the con tours of the pattern piece, for two reasons: (1)
you can use a hoop even near the edge of the piece; and (2) if any puckering
occurs, you can sometimes make adjustments in cutting out the piece, whereas
if you had cut the piece first and then stitched it, the puckering would
be unalterable (Fig. 2-7).

Fig. 2—7 Embellish garment before cutting out: First cut a large rectangle
around the pattern piece; embellish the garment piece before cutting the
contours.
To do this, first cut off the excess tis sue paper around the pattern piece,
anchor it with weights or pins, and trace around with pencil or tailor’s
chalk. Re move the pattern piece and machine- baste the lines you drew, so
you can see them on the underside and so that bias edges are not stretched.
Cut a large rectangle around the garment, allowing at least two inches (5.5
cm) of extra fabric all the way around. Transfer your design to the appropriate
place on the garment piece and do the stitching. Then press on the wrong
side, so you won’t flatten the stitching. Put the original pattern piece
over the fabric. Draw new outlines if the fabric has shrunk slightly because
of the embroidery. Then cut out the actual contours of the garment piece.
Top and Bobbin Tensions
Before you try a straight stitch on your fabric, run a line of it on your
test cloth: set up a small rectangle of the same fabric you’re sewing on and try a line of straight stitch on it. Does it pucker the fabric? Are you
happy with the stitch tension? What does it look like if you tighten the
top tension? Loosen the top tension? Tighten the bobbin tension? Loosen it?
If you have never manipulated your tension set tings, this is the time to
experiment, because the rest of the guide constantly involves adjusting the
settings. Don’t worry if your machine can only, say, manipulate top tension.
Work within your machine’s limits—but find out what they are by playing.
Most machines have a midway point for both upper and lower tension set tings.
When both indicators are set at these midway points and you have the same
thread in top and bobbin, you have what I call a universal tension set ting.
If you don't know how to loosen your bobbin tension, consult the instruction
manual for your sewing ma chine or ask your dealer.
The bobbin tension of some machines is preset in the factory. Therefore,
the instruction manual will tell you not to fiddle with bobbin tension. If
you want to explore the full range of effects possible with machine embroidery,
ignore the manufacturer’s warning. Put a dot of nail polish on the bobbin
to mark the factory setting. Specific details on what to do are in Section
4. For now, merely manipulate top tension and play with different weights
of thread in the top and bobbin; remember that the heavier thread tends to
pull the lighter thread to its side of the fabric.
If no tension setting seems to keep the fabric from puckering, put a piece
of stabilizer (interfacing, tear-away, pa per, or organza) under the test
cloth and try again. As you change the tension settings for the test cloth,
write them down directly on the cloth.
Threadless Practice
The first time I ever sewed on a ma chine, I was given a sheet of printed
straight lines and spirals, both curved and squared. Using an unthreaded
ma chine, I sewed slowly and carefully along the lines. It taught me to take
my time and to watch the stitch that was being formed, at the same time looking
ahead to where the needle would enter the fabric next. I learned to vary
the speed at which I sewed, slowing for curves, turns, and intricate places, and speeding up on the long lines of straight stitch (Fig. 2-8). If you haven't had much practice sewing on the machine, you might want to copy your
cartoons onto typing paper and then practice stitching the main lines with
an unthreaded machine. If you’re satisfied with your work, you could then
use the paper to transfer the design to fabric, via the tailor’s chalk method
(see section 1).
If you have a European or Japanese machine, take the time to make a stitch-length
sample (Figure 2-9). This will tell you how many stitches per inch each setting
makes.
Avoiding Headaches
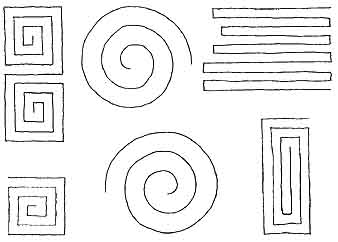
Fig. 2—8 Practice stitching control on these simple patterns.
Remember to save yourself head aches by holding the threads together behind
the presser foot as you begin to sew. Otherwise, the fabric is sometimes
dragged through the needle plate into the bobbin-case area, and valuable
time and psychic energy is lost in unsnarling the mess (Fig. 2-10). And do
yourself a favor: anytime you hear the machine making horrible noises, stop
sewing and investigate. Don’t keep sewing, hoping the noise will go away.
Usually the culprit is a thread in the wrong place.
When you spend hours at the ma chine, your comfort depends on your posture and the way you hold your arms and fingers. If you slump, and at the same
time flap your elbows in the air like pelican wings, you will have a backache and be exhausted in a short time. Hold yourself erect, with a straight spine and tight abdominals. Lean forward from your hips. Rest your elbows on the
sewing surface and place your fingers as shown (Figure 2-11). Experiment
to find the ideal height for your machine. I like my portable ma chine about
three feet above the floor. When I perch on a stool, my machine embroidery
is about chest-high, up where I can see it. I don’t have to hunch over at
all.
I don’t wear glasses, however. If you do, you may need to change the distance
between your eyes and your work—or change your glasses. Barbara Lee Smith
of Oak Park, IL, also likes her machine on a high worktable (she puts her
foot pedal on a box so that she can still use the knee-lift on her ma chine).
She found that her eyes were about 13” from her work and that she needed
half-frame glasses just for ma chine embroidering. Eye tests are usually
given from about 16”, which may not reveal the problems you have in seeing
work closer than that.
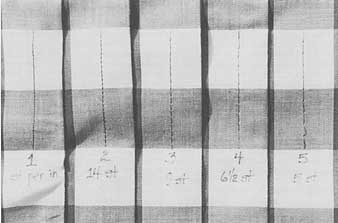
Fig. 2—9 If you’re sewing on a European or Japanese machine, make yourself
a stitch-length sample. If you use 1” gingham, you can easily measure how
many stitches per inch.
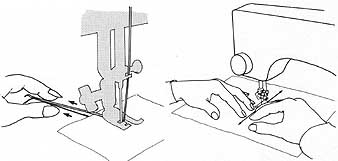
Fig. 2—10 Hold threads together behind presser foot as you begin to sew. Fig.
2—11 Place your fingers in front of the presser foot on either side of the
stitching line.
Straight-Stitch Appliqué
At last, you may begin the machine embroidery. One good use of straight
stitch is for appliqué, and there are at least four good ways to do it (Fig.
2-12).
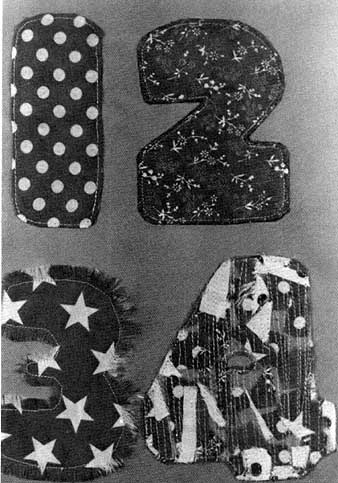
Fig. 2—12 Straight-stitch appliqué four ways: (1) turn under edges 1/4” and topstitch near edge; (2) hidden appliqué (see text); (3) cut appliqué
with no seam allowance, top stitch 1/4” from edge, and deliberately fray
edges; (4) sew back and forth over tiny scraps, cut out the appliqué, and sew it to the backing.
Method 1: Cut out your shapes with a ¼” (6 mm) seam allowance and then straight
stitch along the seam line, so that when you clip the curves and press the
seam allowance under, the edge is crisp and neat. Pin the shape to its backing,
using a glue stick on the back of the appliqué or lots of pins to keep the
fabric from shifting while stitching, and sew 1/8” (3 mm) away from the turned
edge (Fig. 2-13). If you do a lot of this, check the feet that came with
your machine and check with your dealer— there may be a special foot that
helps guide the fabric evenly (e.g., blind hemmer, topstitching foot, etc.).
By holding your fingers as shown in Fig. 2-11, you will prevent the fabric
from puckering. When you reach sharp turns in the shape, stop the machine
with the needle in the fabric, lift the presser-bar lever, and turn the fabric
slightly so that the presser foot is aimed in the right direction. If you
force the fabric under the presser foot at turns, you may stretch the material
on the bias, which results in unsightly bulges (Fig. 2-14).
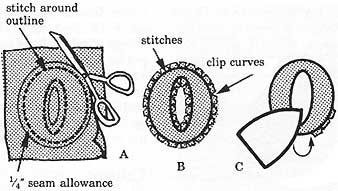
Fig. 2—13 Making an appliqué. A. Add a seam allowance around your pattern.
B. Clip curves. C. Press seam allowance under before you appliqué.
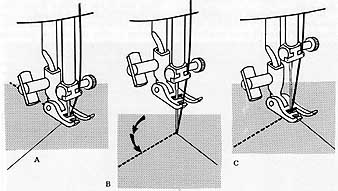
Fig. 2—14 Turning a corner correctly. A. When you reach a sharp turn...
B. Stop with needle in fabric, raise presser foot lever, and turn fabric.
C. Lower presser foot and continue stitching.
Method 2: A second method for straight-stitch appliqué is to cut the appliqué
shape with a 1/4" (6 mm) seam allowance. The same shape is cut from lightweight
fabric. Seam the two shapes right sides together all around the edges. Clip
curves. Cut a slash in the middle of the lightweight fabric. Pull the appliqué
fabric right side out through the slash. Press edges. Sew appliqué shape
to backing fabric with straight stitches. This handy method is called “hidden
appliqué”. (Be careful on light-colored fabric — sometimes the slash shows
through the appliqué.)
Method 3: In the third method, the edges are left deliberately frayed as
part of the design. Cut appliqué shape with no seam allowance. Topstitch
¼” (6 mm) in from the edge. Use a pin to fray the edges.
Method 4: And finally, a method I learned from Peggy M., who is clever at
using ordinary scraps in innovative ways: lay small scraps of fabric on a
foundation (old sheet, muslin, etc.). Sew back and forth with close rows
of straight stitch. Bond iron-on interfacing or fusible web to the back of
the fabric and cut out your appliqué shape. Topstitch it to the backing.
If you are not bonding the back of your appliqué and your piece will receive
heavy wear (such as washable clothing), you must be concerned about matching
grain lines. Try to cut out your appliqué shapes so that when they are pinned
to the backing, the grain lines of both the appliqué and backing are lined
up. For example, I once made an appliqued butterfly, fluttering at an angle
on the backing fabric. Instead of cutting out the butterfly on the straight
grain of the appliqué fabric, I cut it on the bias so that when I pinned
it at an angle on the backing, the grains would line up, as indicated by
the arrows in Fig. 2—15.
How do you handle enormous appliqué shapes, say for a bedspread or wall
hanging? First of all, work on a flat surface when you are pinning the appliqués
to the backing, so everything will lie flat. Pin liberally or fuse by web,
gluestick, or disappearing basting tape, so the fabric won’t shift as you
sew. Keep your hands to the sides of the fabric, using your fingers as guides,
as shown in Fig. 2—11. You can backstitch the first and last stitches, but
I prefer to pull the ends to the back and tie off in knots. When you have
a large number of ends to finish, however, you may want to pull them to the
back and put a spot of fabric glue on them, which will hold through repeated
washings.
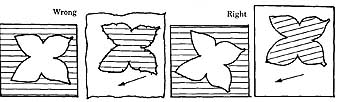
Fig. 2—15 To\ avoid puckering, make sure to cut out the appliqué so
its grain will match the grain (arrows) of the backing fabric.
Crosshatching
Crosshatching is an easy way to fill in large areas with color or texture.
It is done by laying intersecting lines of straight stitching on top of each
other in a grid. The following description of how to crosshatch is accurate,
but it makes an easy maneuver sound complex. Study the pictures and try not
to be boggled by the text.
Stitch down a line. At the bottom, leave the needle in the fabric, raise
the presser-bar lever, turn the fabric 90-degrees, and lower the presser-bar
lever. Take one or two stitches. Repeat the procedure by leaving the needle
in the fabric, raising the presser-bar lever, turning another 90 degrees,
lowering the presser-bar lever, and stitching another long line of stitches.
Use your presser foot as a spacing guide between rows of stitches. It’s hard
to declare how far the second line should be away from the first line because
the length of your stitches at the bottom of each row determines how far
away you will be from the first row of stitching. Maintain this spacing to
keep your lines parallel. When you have finished a rectangle of parallel
stitches, turn the fabric 90 degrees and stitch rows of straight stitch,
perpendicular to the previous rows (Figs. 2-16 and 2-17).
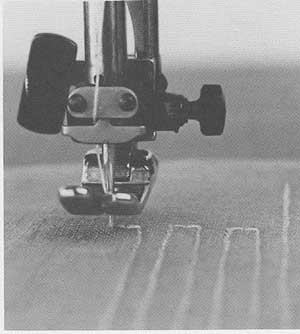
Fig 2—16 Fill-in areas with crosshatching. Begin by stitching parallel
lines, pivoting 90 degrees at each end.
It is annoying to run out of bobbin thread halfway through crosshatching
a project, so start with a full bobbin. Since you won’t see the bobbin thread,
use up old spools and odd colors of thread. The finer the thread, the more
you can get on the bobbin, the less often you will have to change the bobbin.
Crosshatching can also be done in an irregular manner by using the back
stitch lever on a machine (Fig. 2-18).
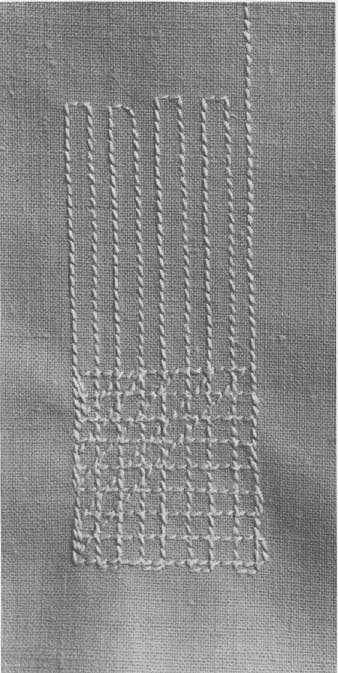
Fig. 2—17 Cross each line with perpendicular lines of crosshatching.
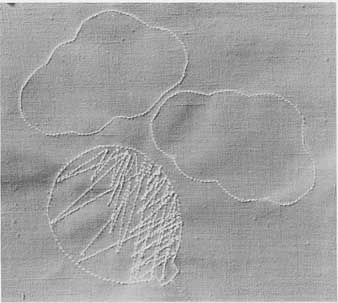
Fig. 2—18 Use the backstitch lever or dial on your machine to fill in
areas with irregular cross hatching.
Since we use a straight-stitch cross- hatching for texture, choose a thread
that has some sheen to catch the light. If you do row upon row of stitching
with 100% cotton, the effect will be lost and you might as well use checked
fabric. But if you use polyester, thin silk, or rayon thread and perhaps
play with the color changes of variegated thread, you create the vibrant
feeling characteristic of all embroidery.
A hint: I once tried filling in small shapes, such as initials and little
flowerpots, with crosshatching. With all the irregular turns and twists in
the shapes, I nearly pulled my hair out from frustration. Then I realized
that it would be easier to make a large rectangle of crosshatching, with
long lines of stitching. After bonding a piece of iron- on interfacing or
fusible web to the back of this rectangle, I cut out my small shapes and appliquéd them by machine to a backing. The bonding kept the edges from fraying
(Fig. 2-19).
This method works particularly well for lettering. If you design the letters
to touch each other, you can appliqué them in one operation, as if they were
script.
Some people like to use cello-tape in stead of pins to hold appliqué to
a backing, stitching right through the tape and later pulling it off. I can't recommend cello-taping these letters to the backing when the edge is so vulnerable
to fraying. When you pull the tape off, it destroys your bonded edge. But
cello- tape works well for nonwovens like leather and vinyl.
Quilting
Quilting with the presser foot on is best done for items with straight lines
or broad, sweeping curves. Otherwise, the fabric begins to creep and before
long, puckers will be caught on the front and back of the piece. (If your
ma chine has adjustable presser foot tension, use it; also see Section 12
for quilting with the darning foot. For a more thorough discussion of machine
quilting, consult our guide, The Complete Guide to Machine Quilting, listed
in the bibliography.) I once quilted an enormous piece of striped fabric
for a king-sized bedspread. I worked on a ping pong table to support the
fabric and loosened both top and bottom tensions slightly to accommodate
the extra thickness of top, batting, and bottom. I also stitched on top of
adding machine tape to keep the fabric from creeping.
Today I heartily recommend using a walking foot when machine quilting with
the presser foot on (Fig. 2-20). It keeps all the layers from creeping. Ask
your machine dealer to show you the proper walking foot for your machine.
You may have to use a foot made for another brand of machine.
Trapunto is the name of another form of quilting in selected areas. Back
a fabric with organza or muslin and straight stitch around a shape on the
topside of the fabric. Turn the fabric over and slit only the organza. Stuff
batting, felt, or yarn (depending on whether the article is washable or not)
into the opening and pad the area evenly. Don’t overstuff it or the fabric
will pucker. Either cover the slash with iron-on interfacing or sew up the
slash in the organza by hand, using a whip-stitch or a catch-stitch (Fig.
2-21).
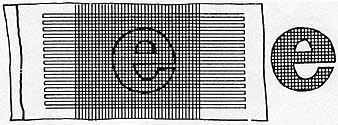
Fig. 2—19 Crosshatch fabric first. Bond to iron-on interfacing. Then
cut out your appliqué.
Additional Ideas
* Copy the decorative design on an old sewing machine. Blow it up slightly and simplify it for appliqué. Using non-frayable but washable fabric such
as knits, appliqué the shapes with straight stitch to the Sewing Machine
Cover in Part Two.
* Using the hidden appliqué method, appliqué bright-colored garden tool
shapes to a ten-pocket tote for gardeners.
* On a length of fabric, draw a mother quail from the side and enough babies
behind her to make a door towel to place at the bottom of a door to keep
cold air out. Quilt the features and outlines with straight stitch.
* Crosshatch a large area of fabric with silk or rayon thread in basket-weave
patterns. Bond fusible webbing to the back of the entire piece. Then cut
out basket shapes and appliqué to a backing. Fill the baskets with fabric
flowers, using the petal shape from Part Two.
* Crosshatch in icy blue and cut out the word “January,” appliquéing it
to a canvas rectangle that's the be ginning of a fabric calendar, and that
will also serve as a sampler of the techniques you’re learning. Watch the
Additional Ideas section at the end of each section for the coming months
of the fabric calendar.
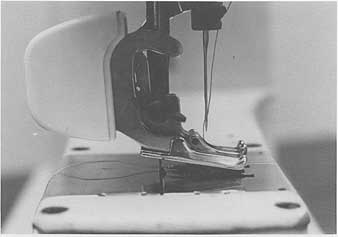
Fig. 2—20 My favorite tool for machine quilting; the walking foot. It prevents
the layers from creeping, causing unwanted puckers.
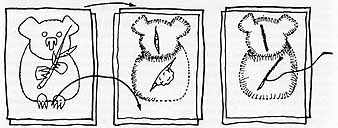
Fig. 2—21 Trapunto is a form of quilting. Back the fabric with organza and outline large shapes with straight stitch. From the back, slash the organza
just enough to stuff the shapes slightly. Then sew up the slashes by hand and finish details with hand embroidery.
|