The old saying that first impressions are lasting ones is especially true
about a home. An attractive, well-maintained exterior says a lot about the
occupants of a house. Whether you are interested in selling your house or
fixing it up to en joy it yourself, an attractive exterior adds value and comfort. A good paint job on the siding and decorative trim and a nicely landscaped
yard make the house look better and also make it a more pleasant place to
be. Well-maintained gutters prevent water damage. A well-maintained surface
on the driveway and walkways makes the house safer and also makes it look
cared for. Plaster and mortar that are in good condition make the house more
watertight, reducing the chance of water damage and improving the appearance
of the house as well. These are just a few of many small and medium upgrades
you can do to keep the exterior of your house safe and in good condition.
Most realtors agree that curb appeal is more important in selling a house
than any of its other features. Although this guide isn’t just about fixing
up a house to sell it, people do move frequently—sometimes when they least
expect to—and a well-maintained home commands the best price because it
shows well.
A new columned arbor is the handsome link that relates the garage
to the house and transforms the entryway to this home.
Small Exterior Upgrades
Maintenance is the most cost-effective way to deal with the exterior
of the house, because most exterior features, such as siding, roofing, and masonry, are expensive to replace. Many exterior maintenance projects
are inexpensive and easy. Like all the small projects listed in this
guide, these upgrades cost less than $900 and can be completed in a day
or two.
Improving Exterior Lighting
For the money, exterior lighting enhances a home and landscaping more
than most other exterior improvements.
The least expensive and easiest system to install is a low- voltage system.
It is also more energy efficient and less expensive to operate than a standard
system, because power is stepped down from the standard 120 volts, in most
cases to 12 volts. The system consists of individual light fixtures and a transformer that plugs into a standard outlet, usually with a timer.
Because the connecting wires carry only low voltage and are waterproof,
they can be strung above ground or buried below ground.
Solar-powered systems are also available. They are more cost-efficient
than standard electric fixtures to install and operate (they don’t use
electricity), which more than offsets their higher purchase price.
Light switches that detect motion and body heat have come down in price
since they originally appeared on the market. Any movement in the area
at which the detector is aimed will turn on the light. As long as the movement
continues, the light will stay on. The switch also includes an adjustable
timer that will shut off the lights automatically after no motion has been
detected for a specified length of time. Carrying out the trash or walking
between the garage and the house at night are both safer with lights that
come on automatically.
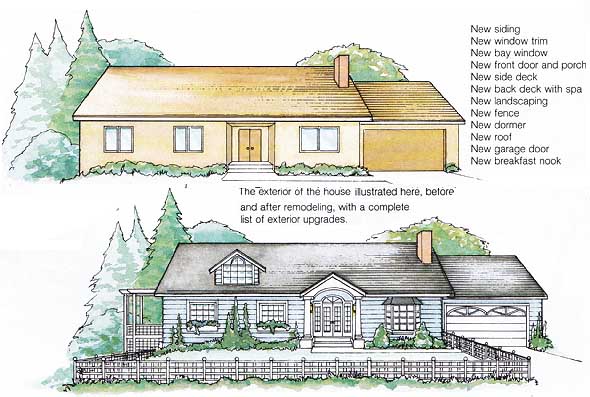
Exterior Upgrades: The exterior of the house shown earlier is illustrated
here, before and after remodeling, with a complete list of exterior upgrades.
- New siding
- New window trim
- New bay window
- New front door and porch
- New side deck
- New back deck with spa
- New landscaping
- New fence
- New dormer
- New roof
- New garage door
- New breakfast nook
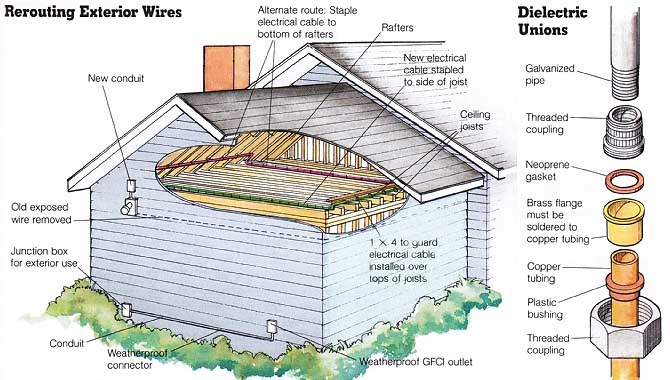
Rerouting Exterior Wires: ; Dielectric Unions:
Repairing Electrical Wiring
Improper wiring can cause fires. All exposed exterior wiring should be
encased in a proper electrical conduit (a metal pipe).
Ideally, exposed wiring should be moved into the attic or basement area.
It is safer there, and moving it indoors avoids unsightly wires and pipes
on the exterior. In most cases, running wiring in the attic or basement
area is less expensive than using conduit on the exterior, since the metal
pipe, the connectors, and the tools required to work with conduit are expensive.
If hiding the wire is not possible, then running a conduit is the only
smart choice left. A 25-foot length of exposed wire can be made safe in
an afternoon. Use waterproof boxes and wire made for use inside conduit.
Never use electrical tape to join and protect wire connections. Electricity
can arc through the tape across two wires (or a wire and the junction box) and could cause a fire. Special wire connectors are made to prevent this
from happening.
Place a weatherproof junction box at the point where the wire exits the
house. Run electrical conduit from the box to the place where the wire
ends. At that point, connect another unction, plug, or light box to the
conduit. String new wire from the first junction box to the last one.
Although the National Electrical Code regulates electrical installations,
the code can be superseded by municipal laws. It is wise to consult local
building officials for advice prior to starting an electrical project.
Repairing Faucets
Leaky faucets can waste a lot of water. Faucet gaskets are usually the
culprit. They have a tendency to hum; the dried gasket vibrates as water
passes over it. You can replace these gaskets in about half an hour at
very little expense. A faulty faucet valve can cause reduced water flow.
For just a few dollars more, you can replace the entire hose bibb or faucet
in about the same time it takes to replace a gasket.
Replacing a faucet is simple. First, turn off the main water inlet valve.
Then unscrew the old faucet (counterclockwise) with two pipe wrenches or
a large pair of channel-type pliers. Having the proper wrench or pliers
makes this an easy task. Finally, wrap the threads of the replacement faucet
with pipe joint tape, or paint them with pipe joint compound, and screw
the faucet into place.
Unclogging Sewer Drains
Root growth and grease build up are the two most difficult intruders to
remove from a sewer drain. If a 25-foot snake won’t clear the drain, chances
are that one or both of these problems exists.
Unclogging such obstructions is a task for professionals. Cleaning sewer
drains improperly can damage the pipes be yond repair, and replacement
can cost thousands of dollars.
If you are thinking of having a sewer-cleaning company do the work, require
them to guarantee that they will replace any pipe that they damage during
the cleaning process. Ask them to give a price for unclogging the drain
before they start the work.
Replacing Clogged Water Pipes
Clogged water pipes, evidenced by reduced water flow through out the house,
not just in one fixture, can't be cleaned. They must be replaced.
Galvanized pipe should be replaced with copper pipe; it lasts longer.
Use dielectric unions where the new copper pipe connects to old galvanized
pipe, to prevent an electrolytic reaction (the deterioration of metal that
results when dissimilar metals come into contact with each other in the
presence of water).
Repairing Cracked Stucco
The most important part of re pairing cracked stucco is blending the repaired
cracks into the existing surface. The type of caulk to use depends on the
thickness of the crack. For cracks less than ¼-inch thick, use a paintable
silicone caulk. It shrinks less than others and remains pliable enough
to withstand movement as the joint expands and contracts with changes in
temperature.
Apply the caulk to the open joint, force it into the crack with a putty
knife, and then use a dampened sponge to match the surface of the caulk
to the stucco surface being re paired. Avoid using too much caulk; a wide
caulked joint can be as unsightly as the original crack.
For cracks larger than ¼-inch thick, use a stucco-patching com pound.
For maximum adhesion, thoroughly clean the crack of all debris and loose
stucco. Then mix and apply the patching compound according to the manufacturer’s
directions.
Keep in mind that patching compound only fills the crack—it does not bond
the broken edges of the stucco—so that any movement of the stucco, due
to settling or earth quakes, will probably cause a crack to open up again.
Repairing Wood Siding
Wood siding that's split or cracked can be mended with exterior-grade
patching com pound. For major damage, use epoxy-based wood fillers. With
the proper technique, the re pair will be invisible. Before mending wood
siding with patching compound or epoxy, it's important to ensure that
the damaged siding is securely fastened. If not, it should be renailed and the new nail holes patched.
To mend smoothly finished siding, use a paint scraper to expose bare wood.
Then, with a 2-inch-wide putty knife, push patching compound into the crack.
At first, while the freshly spread putty is still wet, it will bulge at
the crack. As it dries it will shrink and recede into the crack. Each coat
of patching compound should be applied and then sanded when dry. Two or
three applications will be necessary. Applying the compound too thick in
an effort to hide the crack with one coat can result in a lot of unnecessary
sanding. To prevent the first coat of patching com pound from pulling out
of the crack as you are wiping it onto the wood with the putty knife, dip
the cleaned blade of the putty knife into a container of water and re-wipe
the puttied surface.
To mend rough- or re-sawn surfaced siding, follow the technique for mending
smooth wood, but use a wire brush instead of sandpaper on the patch. The
wire bristles will cut irregular grooves into the dried patching compound,
making the patch less visible.
Replacing Damaged Wood Siding
Siding that's too damaged to be repaired with patching com pound can
be patch-replaced. This involves removing the damaged siding and replacing
it with new material. When a sheet of plywood is damaged, the entire piece
must be re placed, but the removal is easy. Simply use a cat’s paw (nail
remover) to pull out all the nails that hold the plywood in place, use
the removed ply wood as a pattern to cut a new piece, patch the siding
paper with an approved patching compound, and then nail on the new piece
of plywood.
Plank siding is not as expensive as plywood to repair be cause the amount
of wood required for a patch can be restricted to the damaged area. However,
the process is more labor intensive and can damage the siding paper.
To make the repair, cut out the damaged plank with a circular saw. Adjust
the blade depth to /i6 inch less than the thickness of the siding, which
is usually ¾ inch thick. After cutting the material, remove the nails with
a cat’s paw, and then remove the siding and use it as a pattern to make
the replacement piece. The process for replacing plank siding is the same
as for plywood siding. Seal all joints—new and old— with exterior caulk.
If a plumbing pipe penetrates the siding to be replaced, turn off the
water, cap the sup ply pipe, drill the hole in the siding at the pipe location,
in stall the siding, replace the cap with the pipe, and turn on the water.
Trying to cut around a hose bibb will leave a large, unsightly hole in
the siding that will make the repair look unprofessional. Follow a similar
procedure for electrical devices.
If the siding on an entire side of the house must be re placed, this project
could be a medium to large upgrade.
Repairing Roof Leaks
Roof leaks are not expensive to repair, but finding the location of the
leak can be a challenge. For example, water dripping from the living room
ceiling could be coming from a leak over the kitchen. Water has a tendency
to travel along the underside of the roof sheathing and rafters before
finally dripping down into the house. Water stains on the rafters indicate
that a leak exists, but they do not necessarily indicate where the leak
is on the roof.
Finding a leak is not difficult, but it can be time-consuming; hence,
hiring a contractor to find the leak can be expensive. To find a leak yourself,
use a hose to spray small areas of the roof (one 5- or 6-foot-square area
at a time) heavily with water. The smaller the area you spray, the better
your chance of pinpointing the location of the leak. Spray for about ten
minutes in each area; less time may not be sufficient for the water to
pass through to where it can be seen. If no attic exists, and there is
a layer of interior finish material such as wallboard, remove it and expose
the roof rafters. Water can puddle atop the wallboard for 15 to 30 minutes
before beginning to drip through.
For a sloped roof, start at the overhang (the lowest point) and work toward
the ridge (the highest point), being careful not to spray water up under
the shingles. Sloped roofs are not completely watertight and can leak if
water is forced underneath the shingles.
Caution: Be extremely careful when walking on a sloped roof, especially
when it's wet.
Once you have found the leak, replace the shingle or shingles causing
the problem, or use roofing mastic to patch the underlying roofing felt.
If metal flashing is found to be the culprit, liquid solder is the appropriate
patch material.
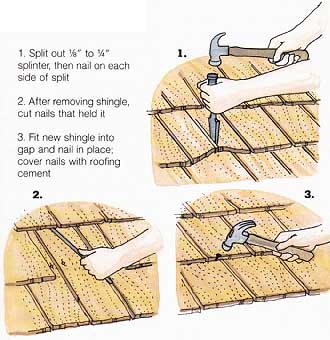
Repairing a Bowed Shake: 1. Split out 1/8” to ¼” splinter,
then nail on each side of split; 2. After removing shingle, cut nails that
held it; 3. Fit new shingle into gap and nail in place; cover nails with
roofing cement.
Caring for Wood Roofs
Keeping wood shingle and shake roofs clean and water- resistant helps
deter leaks. Wood shingles and shakes are easily and quickly damaged by
the sun’s ultraviolet rays. Sun and wind evaporate the natural oils found
in the wood, allowing it to absorb water. The wood then expands, causing
the shingles to split and cup (curl).
Keeping the roof clean also inhibits the growth of mildew and other fungi.
Although moss, leaves, and other debris don’t damage wood roofing material,
they trap moisture that can cause damage. The moisture provides an ideal
habitat for fungal growth, such as soft rot, which quickly deteriorates
wood.
The easiest way to clean a roof is to power-wash it. The best time is
in the fall, before heavy winter weather begins. Be careful not to force
water underneath the shingles. Every third year, follow the washing with
a light spray of shingle and floor oil. Be sure that it's specified for
roof applications and meets local fire requirements. The oil keeps water
from traveling deep into the wood and helps prevent cup ping and splitting
by keeping the shingles soft, pliable, and water-resistant. Mixing a small
amount of paint pigment, available in a range of colors and sold in tubes,
into the oil will ward off damage caused by ultraviolet rays.
Caution: Be extremely careful when walking on an oiled sloped
roof. When oiling a roof, it's wise to be tied to the other side of the
roof with a sturdy safety rope.
Cleaning is an important part of roof maintenance. To prolong the life
of your roof, it's also important to replace shingles that are beyond
repair and to treat the roof with a preserving chemical. This should be
done every five years. Once the roof is clean, replace split and damaged
shingles. Finally, apply a chemical to the entire roof to preserve and protect the shingles. Either an oil-based or a water-based solvent can
be used to carry the chemical. In dry climates the oil-based solvents are
better. The chemical used to help pre serve wood shingles is an approved
pesticide (such as copper naphthenate), so take care to apply it properly.
Paint pigment is purchased separately and added to the chemical to hide
the green cast left by the pesticide and to blend the new shingles into
the rest of the roof.
Using a reputable roof maintenance company is an alternative to doing
it yourself. It is important to hire a firm that offers a five-year unconditional
guarantee. Roof maintenance done correctly every five years can save 40
percent over the cost of replacing a roof. Painting roof shingles may void
any warranties and is not recommended.
Cleaning Gutters and Downspouts
Gutters and downspouts are designed to prevent rainwater from falling
onto the ground near the foundation of the house. This preventive mea sure
is important because wet soil adjacent to a foundation undermines the support
needed for the foundation to remain stable. Downspout drain leaders should
extend at least 3 feet from the foundation before draining onto the ground.
Many communities re quire downspouts to drain into an underground piping
system that carries all rainwater into a local storm drain system.
As a point of information, the storm drain system and sanitary sewer system
are usually separate entities. Sewer systems are supposed to route waste
to treatment plants; storm drain systems usually drain into nearby rivers,
streams, or settling ponds, moving flooding to a safe place outside the
community.
If gutters and downspouts aren’t kept clean, water will overflow onto
the ground adjacent to the foundation, and the foundation may shift as
a result. When the house shifts, walls crack, floors buckle, and windows and doors don’t operate smoothly. Preventing this problem is as easy as
sweeping and hosing out gutters and downspouts at the end of fall, and adding leaders to the end of the downspouts to carry water a minimum of
3 feet away from the foundation.
Solving Grading and Drainage Problems
If floors are squeaking or buckling, windows and doors are not operating
properly, or plaster is cracking, the problem may originate with an unstable
foundation.
A house is only as stable as its foundation, and a foundation is only
as stable as the soil on which it rests. When the moisture content of the
soil is excessive due to poor drainage, the entire house is affected.
Proper grading is essential for good drainage. All surfaces (dirt, concrete,
brick, and so on) within 30 inches of the perimeter of the house must slope
away from the foundation at 1/4 inch of fall for each linear foot of travel.
Otherwise, water will settle around the foundation and can cause it to
shift.
On flat building lots (as op posed to hillside property), proper grading
is usually all that's needed. However, in some situations an under ground
French drain can be used to carry water away from the foundation (see illustration).
Even on flat in-town lots, the ground must be graded to slope slightly
so that water will run off toward municipal storm drains.
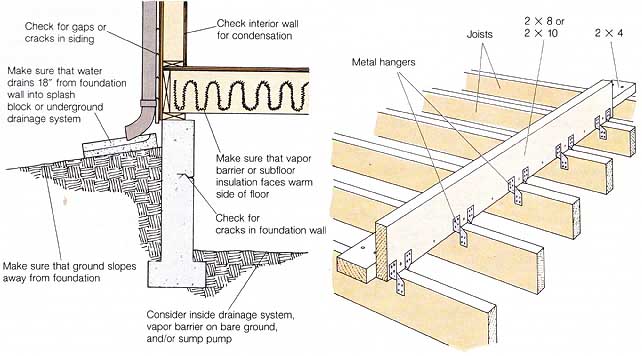
Checking for Moisture Problems: Check for gaps or cracks in siding,
Consider inside drainage system, vapor barrier on bare ground, and /or sump
pump, Make sure that water drains 18” from foundation wall into splash
block or underground drainage system; Constructing a Strongback: An Alternative
to Straightening Ceiling Joists
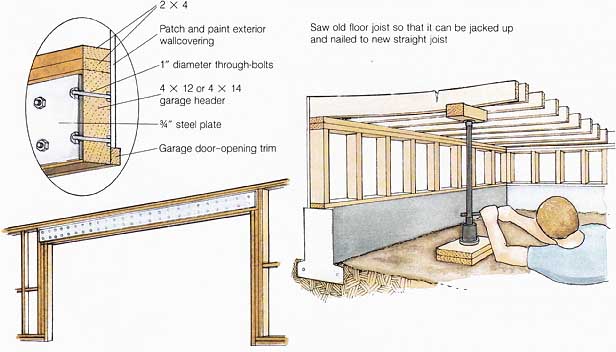
Fixing a Sagging Garage Door Opening: 2X4, Patch and paint exterior
wallcovering, 1” diameter through-bolts; Fixing a Sagging Floor: Saw
old floor joist so that it can be jacked up and nailed to new straight
joist
Controlling Structural Pest Damage
Eliminating earth-to-wood con tact is an almost cost-free project that
can reduce the possibility of rot and termite infestation.
The Uniform Building Code requires earth to be at least 6 inches away
from any wood in the home; the Federal Housing Administration requires
8 inches. There are two reasons for eliminating earth-to-wood contact:
Earth in contact with wood (or any cellulose material) attracts termites and related pests and gives them direct access to a food source; and wet
earth in contact with wood promotes fungus growth, which causes wood to
rot. It begins when the wetness of wood reaches 20 to 30 percent.
To eliminate earth-to-wood contact, remove all earth (including planting
bed areas and cellulose debris) within at least 6 inches of all wood structures.
Most stucco exteriors have wood behind them near their base and should
be dealt with like wood siding.
If a fence butts up against the exterior wall of the house, add flashing
in the form of a thin layer of galvanized sheet metal between the fence and the house, to keep termites from traveling from the fence into the
exterior siding and then into the structure.
If no earth-to-wood contact exists, finding termite trails is easy. Termites
avoid light and prefer to travel from the earth into a home through tunnels
that they create from mud. It is wise to inspect the exposed subarea frequently
for mud tunnels. They are about the size of a pencil and can be found against
the inside of the foundation wall between the ground and any nearby wood.
If you find termite tunnels, call specialist in structural pest control
to exterminate the termites.
Fixing Deteriorating Posts
Wood posts that sit directly on concrete, such as posts that support patio
or porch covers, can deteriorate after several years. The post absorbs
rain and irrigation water, fungus damage begins, and the post starts to
rot at the bottom.
Repair is easy. First, brace whatever the post is supporting with temporary
posts; then cut off the lowermost inch of ye post with a handsaw, and paint
the cut with wood preservative. Reconnect the post to the concrete with
a sheet-metal post base (with spacer). Move the cut post out of the way,
attach the post base with concrete nails, and then place the spacer in
the base, followed by the post. Remove the temporary brace, and finally
nail the top of the post base securely to the post. The spacer inside the
post base supports the post far enough above the concrete to deter future
capillary action, keeping the post dry and ex tending its life.
Fixing Sagging Garage Door Openings
In an older home a sag may occur in the garage door header, the horizontal
wood timber above the door that makes up the top of the opening. A sagging
header is caused by either the weight of the roof or the weight of the
floor above the garage door. Once the header has sagged, it must be either
replaced or raised and braced with a, steel plate.
As a do-it-yourself project, replacement is by far the more cost-effective
option because this project is labor intensive. If done by a professional,
this would be a medium upgrade.
Use temporary supports to hold the structure in place while the header
is being re placed. Cut all nailed connections, using a reciprocating saw
with a metal-cutting blade. Remove the header and use it as a pattern for
its replacement. The replacement timber should be the strongest grade of
lumber available—select structural.
If the work will be done by professionals, adding metal bracing can be
more cost- effective than replacing the header, because less labor is involved.
If you choose bracing, contact a structural engineer to determine the thickness
of the steel plate and the number and size of the bolts to be used to make
the repair with a steel-plate brace.
Fixing Other Sagging Framing Members
Floor, ceiling, and roof framing members can also sag after being in place
for many years. The fibers tear at the lower side of the horizontal framing
member as a result of the weight from above. With roof rafters and ceiling
joists, the weight of the roof can cause this to hap pen. With floors,
furniture or load-bearing walls can be the culprit.
Once a horizontal framing member has sagged and completely dried out,
its shape is almost permanent. To repair it, cut the sagging member at
its lowest point, raise it to a point slightly higher than its original
position, and then sister (glue and nail or bolt) a new framing member
alongside it.
When sistering a new horizontal framing member to an old one, it's wise
to use a larger size for the sistered piece when possible; it will be stronger and resist sagging more effectively. For example, you would sister a 2
by 8 floor joist with a 2 by 8, 2 by 10, or 2 by 12 if space allowed.
Upgrading Concrete Flatwork and Blacktop
Walkways and driveways with cracked concrete or potholed blacktop can
be unsightly and dangerous. Damage usually occurs when the earth below
heaves or shifts, a condition usually brought on by extreme drying, as
from a drought, by excessive moisture, or by alternate freezing and thawing.
If no drought exists, chances are that excessive landscape irrigation
water or wet weather are causing the damage. Once it occurs, the additional
openings in the surface allow even more moisture to permeate the ground
below. Patching com pounds, which are formulated to expand and contract
with changes in temperature at the same rate as the concrete or blacktop,
can help to prevent continued water seepage. Be aware, however, that patching
compounds are not permanent and will require continued maintenance. In
addition, it may be difficult to match the original color.
Concrete is cracked beyond repair when patches don’t hold, existing cracks
widen, new cracks develop, and major shifting occurs. If you want to replace
the concrete, have a soils (or geotechnical) engineer recommend a method
of replacement. For example, before pouring the new concrete, digging out
6 to 8 inches of earth and replacing it with compacted rock could reduce
the chance of future cracking. Installing a grid of ½-inch steel rebar and using a mix of concrete that contains more cement than usual might
also help.
Blacktop sealer protects blacktop against weather dam age. To repair small
cracks in blacktop, brush out any loose matter and fill the cracks with
butyl cement. Smooth the top with a putty knife. Fill large cracks and holes with blacktop patching compound, packing it down with a shovel or
tamp. Lay a board over the area, and drive on it with your car to compact
it completely. See illustration at right.
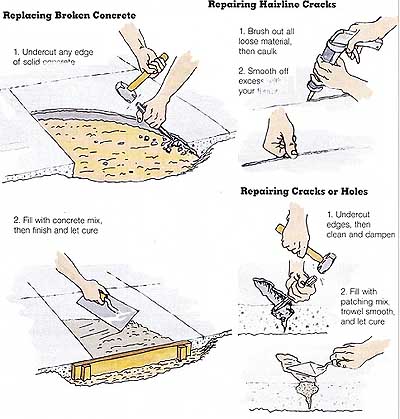
Repairing Damaged Concrete: Replacing Broken Concrete: 1
Undercut any edge of solid concrete; 2. Fill with concrete mix, then finish and let cure. Repairing Hairline Cracks: 1. Brush out
all loose material, then caulk; 2. Smooth off excess. Repairing
Cracks or Holes
Patching Concrete Foundations
Foundation cracks can be unsightly but may not indicate serious damage.
When you notice cracks (hairline or other wise), it's best to consult
a structural engineer to ensure that a serious problem does not exist.
For do-it-yourself cosmetic repairs of cracks that are not serious, use
latex concrete patching compound. The easiest type is already mixed, although
patching compound is also available in powdered form that you mix with
water.
Maintaining Exterior Caulk
Maintaining caulk on the exterior of the house is an easy, an expensive
face-lift that can save thousands of dollars. Caulk is used to create a
water seal at joints, especially around windows and doors. Eventually,
the caulk dries out, causing it to shrink and crack. Water can then reach
framing members, which can result in serious fungus damage.
The best kind of caulk for the exterior of the house is paintable silicone.
Silicone caulk was not available when older homes were built; latex caulk,
which dries out, was used then instead.
The most obvious caulked joints in a house are wood-framed windows where
the glass fits into the frame and is sealed with glazer’s putty. Unlike
other caulk, glazer’s putty becomes extremely brittle after it has been
in place for several years. Since removing the brittle putty could result
in cracked window panes, simply rough up the old putty with a wire brush, and then apply new putty with a putty knife. If the old putty has been
painted, re move all paint before applying the new putty.
Glazer’s putty has a linseed- oil base, and therefore is water- resistant.
However, it will last longer if it's painted.
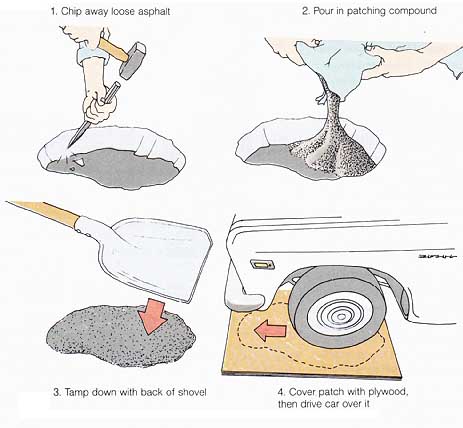
Repairing Holes in Blacktop: 1. Chip away loose asphalt; 2. Pour in
patching compound; 3. Tamp down with back of shovel; 4. Cover patch with
plywood, then drive car over it.
Insulating Walls, Ceilings, and Floors
You can make your home more comfortable and reduce heating and cooling
costs by adding insulation to walls, ceilings, and floors. This upgrade
is not done to the exterior of the house (although adding wall insulation
can be done from the outside), but it affects the building envelope and is there fore considered an exterior upgrade.
Insulating floors and ceilings that are accessible by a crawl space or
an attic is an easy do-it-yourself project. Insulation is relatively inexpensive
to buy and simple to install.
Batt insulation is the best type. It comes in rolls in widths designed
to fit between framing members that are either 16 inches or 24 inches on
center. You can cut the insulation to length or to odd widths with a utility
knife or a pair of scissors.
Foil-backed insulation is not recommended, because condensation occurs
at the foil layer, which can cause water damage. Paper-backed or back less
insulation is better. If you use paper-backed insulation, place the paper
toward the in side of the house.
In the attic, simply lay insulation in place; pierce the paper backing
if you are installing it over existing insulation. In the basement area,
position insulation between the floor framing members, and hold it in place
with flexible rods, baling wire, or fiberglass netting nailed to the bottom
of the floor framing members.
Use caution when working with fiberglass insulation to prevent the minute
glass particles from entering the body or becoming embedded in the skin.
Wear a breathing mask to keep from inhaling the particles, use goggles
for eye protection, and cover the entire body (including the head) with
clothing. Use duct tape to seal clothing at the neck, wrists, and ankles.
Note: For walls and for ceilings where no attic exists it's best to have
a professional in stall insulation. This project qualifies as a medium
upgrade; special equipment is required to blow cellulose insulation into
the wall and ceiling cavities. Keep in mind that fiber glass insulation
is more resistant to moisture than cellulose insulation and if installed
properly will last longer.
Controlling Air Infiltration
Insulating without controlling air infiltration is like trying to bake
without closing the oven door. Infiltration control includes weather-stripping
doors and windows, sealing penetrations between the basement area and the
living area above, sealing penetrations between the attic and the living
area below, and installing gaskets or sealing all penetrations in exterior
wallcoverings.
Infiltration control is even less expensive than insulating and is easier
to do. Canned spray foam, scraps of sheet metal, and rubber switch-plate and outlet gaskets are the materials used. For example, in the attic or
basement area, you can seal large holes at pipe or duct penetrations with
a scrap of sheet metal; seal smaller openings with expanding spray foam.
To seal heat-register covers in walls, floors, or ceilings, remove the
cover, fill the gap between the supply duct and the wallboard with foam, and replace the cover.
To find penetrations in a previously insulated attic, use a lighted candle.
Air escaping from the living area below exerts pressure as it passes through
small holes into the attic—sometimes with enough force to extinguish the
candle but always with enough to cause the flame to flutter. Be careful
when performing this test, and carry along a small fire extinguisher.
A surprising amount of air can enter a house through switch plates and electrical out lets. Installing gaskets under these covers is an easy,
inexpensive, cost-effective upgrade that will help to eliminate air infiltration.
The gaskets are available at hardware stores. Simply remove the switch
plate or outlet cover, install the gasket, and replace the cover. You can
reuse the original screws that hold the cover in place— the rubber gaskets
are thin.
Although any kind of weather stripping is better than none at all, weather
stripping that's attached with nails or screws is far superior to the
pre-glued stick-on type. For doors, the most effective (and most expensive)
weather stripping is the interlocking type. Some companies specialize in
the installation of inter locking weather stripping.
Doors and windows should be weather-stripped where the fixed frame meets
a moving part (on the top, bottom, and both sides). Double doors should
also be weather stripped where the two doors meet in the middle.
Cleaning Chimneys
Fireplaces that are used frequently, especially those that are fueled
with resinous wood such as pine or fir, cause a greater creosote buildup
in the chimney than less frequently used fireplaces or those in which hardwoods,
such as oak, ash, or walnut, are burned. Creosote is a by-product of combustion
that adheres to chimney walls. It is flammable and under certain conditions
can be explosive. It should not be allowed to build up in the chimney for
long periods of time.
A chimney sweep can thoroughly inspect and clean a chimney in a few hours.
See the illustration above to do it yourself. If cracks are found in the
masonry, have a licensed or certified professional do the re pairs. Do
not use the fireplace until the repairs are completed, since cracked masonry
can cause a house fire.
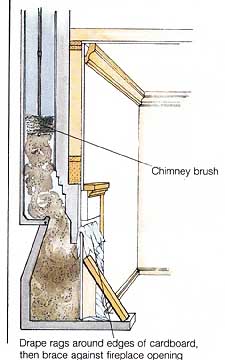
Cleaning a Chimney: Drape rags around edges of cardboard,
then brace against fireplace opening.
|